Pneumatic tubing, an essential component in the realm of industrial automation, offers a seamless method to transport pressurized air within systems. Its significance in improving efficiency, reducing system costs, and enhancing operational safety cannot be understated. Companies continually seek innovative improvements in materials and design to maintain a competitive edge, ensuring pneumatic tubing remains a staple in modern industry.
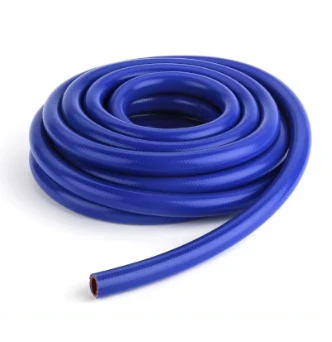
Drawing from years of hands-on experience, it is clear that selecting the right pneumatic tubing directly influences the performance and longevity of pneumatic systems. Industry experts consistently emphasize the importance of understanding both the application's specific requirements and the tubing's material properties. Traditionally, pneumatic tubing materials include polyurethane, polyethylene, and nylon, each presenting unique properties suited for different environments.
Polyurethane tubing stands out due to its flexibility and resistance to kinking, making it ideal for dynamic applications where movement is frequent. From maintaining machinery in automotive production lines to precise movements in robotics, polyurethane’s versatility is unrivaled. Its remarkable resistance to abrasion and chemicals ensures durability even under harsh conditions, thus validating its widespread use across industries.
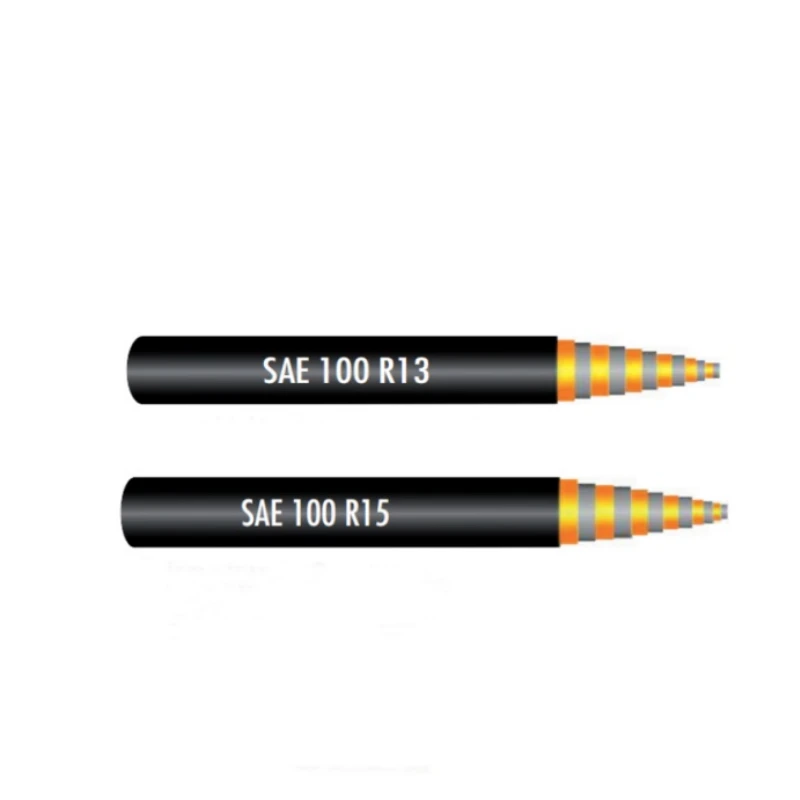
On the other hand, polyethylene tubing is recognized for its lightweight characteristics and cost-effectiveness. Its ease of installation makes it an ideal choice for applications that require quick setups and modifications. While its temperature range and pressure capacity are less extensive than other materials, for applications such as pneumatic controls and instrumentation lines, polyethylene fits perfectly within those constraints.
Nylon tubing presents a higher tensile strength and better withstands high temperatures and pressures, making it a preferred choice in aerospace and military applications. Its semi-rigid nature offers exceptional dimensional stability, essential for maintaining calibrated configurations that demand high precision.
The selection process also extends beyond just material consideration. Tubing diameter, wall thickness, and the environment's operating conditions are critical in determining the appropriate tubing. For instance, a system requiring high-flow applications might necessitate tubing with a larger diameter, whereas more stringent environmental regulations could lead to selecting materials that are compliant with specific health and safety standards.
pneumatic tubing
An authoritative understanding of pneumatic tubing includes recognizing the potential challenges encountered during its implementation. Issues like environmental exposure, such as UV rays or corrosive substances, can affect tubing integrity over time. It is where expertise in material science plays a crucial role. Selecting tubing with UV stabilizers or additional protective coatings significantly reduces the risk of degradation. Similarly, for systems operating under extreme temperatures, tubing with enhanced thermal resilience ensures consistent performance without compromising safety.
An often-overlooked aspect is the compatibility of pneumatic tubing with different fittings and connectors, which can heavily influence the system's reliability. Market leaders in pneumatic systems technology advocate for thorough testing and validation processes to ensure that tubing and connectors work seamlessly, thereby mitigating the risk of air leaks which could lead to system failures or efficiency loss.
Real-world experience reveals that preventive maintenance strategies are crucial in extending the life cycle of pneumatic tubing. Regular inspections, coupled with proactive replacement of vulnerable sections, prevent minor faults from escalating into costly operational downtimes. Adoption of advanced diagnostic tools, such as thermal imaging and ultrasonic leak detectors, enhances predictive maintenance capabilities, thereby reinforcing system reliability and trustworthiness.
Aligning expert recommendations with manufacturer guidelines ensures that pneumatic tubing meets or exceeds the expected performance metrics. It fosters a culture of accountability and trust in industrial practices, where invested stakeholders feel confident in their pneumatic systems' capability to support rigorous demands.
In conclusion, pneumatic tubing's intricate role in facilitating modern automation underscores the necessity for informed decision-making supported by authoritative knowledge and experience. Navigating the complex interplay of material characteristics and application requirements enables industries to harness the full potential of pneumatic technology, culminating in efficient, safe, and sustainable operations. As advancements continue to emerge, embracing change while adhering to established principles ensures pneumatic tubing remains at the forefront of industrial innovation.