Non-conductive rubber hoses are essential components in industries where the transmission of electric current must be prevented for safety purposes. These hoses, made from high-quality rubber materials, serve critical functions in environments such as chemical plants, industrial machinery, and even medical equipment. Understanding the nuanced advantages and proper applications of non-conductive rubber hoses can elevate operational safety and efficiency across various sectors.
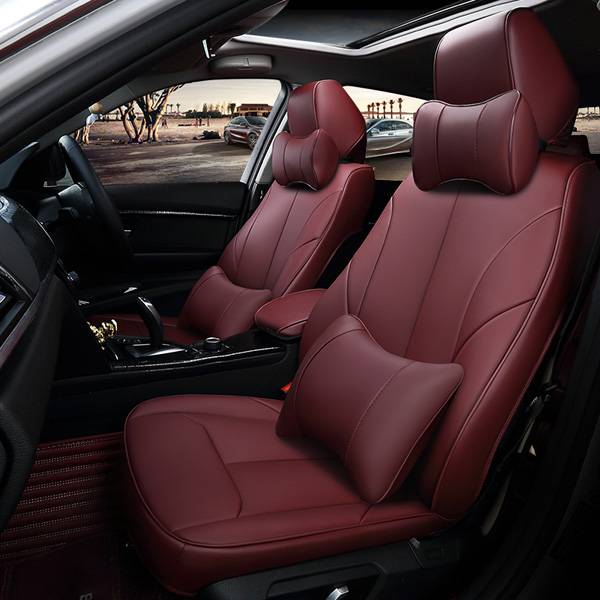
Firstly, the primary advantage of non-conductive rubber hoses lies in their ability to resist electrical conductivity. Unlike their conductive counterparts, these hoses are specifically designed using dielectric materials to prevent the flow of electrical current. The insulation properties make them indispensable in environments where accidental electric shock could be hazardous or fatal. For instance, in industries operating heavy electrical machinery, using non-conductive hoses mitigates the risk of electrical interference and ensures the safety of operators and technicians. This design inherently provides a trust factor that is vital in high-risk industrial settings.
Additionally,
non-conductive rubber hoses boast remarkable durability and flexibility. Manufactured with synthetic rubber compounds, these hoses exhibit impressive resistance to abrasions, chemicals, and harsh weather conditions. Their resilience against diverse industrial chemicals ensures that the hoses maintain their integrity and functionality even in corrosive environments. This characteristic not only offers longevity but also translates to cost-effectiveness, as frequent replacements are minimized. Companies investing in non-conductive hoses thus benefit from reduced downtime and maintenance costs, positioning these hoses as a reliable partner in operational excellence.
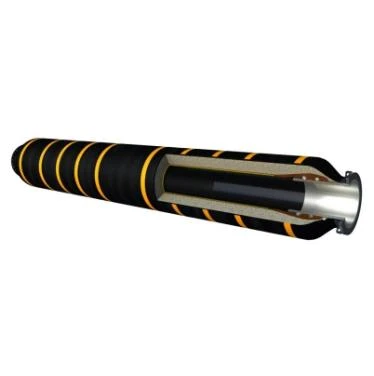
From an expert standpoint, proper installation and regular maintenance of non-conductive rubber hoses are paramount. Ensuring that these hoses are appropriately fitted with suitable connectors and regularly inspected for wear and tear guarantees their optimal performance. Professionals advocate for routine checks to identify potential damage, such as cracks or hardening, which could compromise their non-conductive properties. Implementing a maintenance schedule guided by industry standards not only prolongs the lifespan of the hoses but also fortifies the safety standards of the facility.
non conductive rubber hose
The authority of non-conductive rubber hoses in their respective sectors is underscored by their compliance with stringent industry standards. These hoses are constructed according to benchmarks established by organizations like the International Electrotechnical Commission (IEC) and various national safety authorities. Compliance with such regulations entails rigorous testing for dielectric strength, pressure tolerance, and flexibility, ensuring that they meet the expected safety and performance metrics. Such stringent adherence to standards underscores the trustworthiness of non-conductive rubber hoses as a staple in secure industrial operations.
In practical application, non-conductive rubber hoses are integral to processes such as pneumatic and hydraulic systems, where precision and safety are paramount. These hoses serve as conduits for compressed air, steam, water, and various chemicals without risking the inadvertent conduction of electricity. By choosing non-conductive solutions, industries safeguard sensitive components and personnel, maximizing productivity without compromising on safety. Moreover, these hoses are adapted to a variety of fittings and sizes, making them versatile in construction, marine, aerospace, and automotive sectors as well.
In conclusion, non-conductive rubber hoses represent an intersection of safety, reliability, and performance. As industries continue to advance and innovate, the demand for non-conductive solutions reflects a commitment to maintaining safe and efficient work environments. Their intrinsic properties, bolstered by adherence to rigorous standards and expert maintenance practices, reinforce their role as indispensable components in mitigating electrical hazards. Organizations that leverage the unique benefits of non-conductive rubber hoses not only enhance operational outcomes but also demonstrate a proactive stance in workplace safety.