The landscape of industrial and domestic applications often necessitates the use of high-pressure rubber hose pipes, which are vital for efficient fluid and gas transmission. Recognized for their robustness, flexibility, and ability to withstand extreme conditions, these hoses are indispensable across a myriad of industries including automotive, agriculture, and construction.
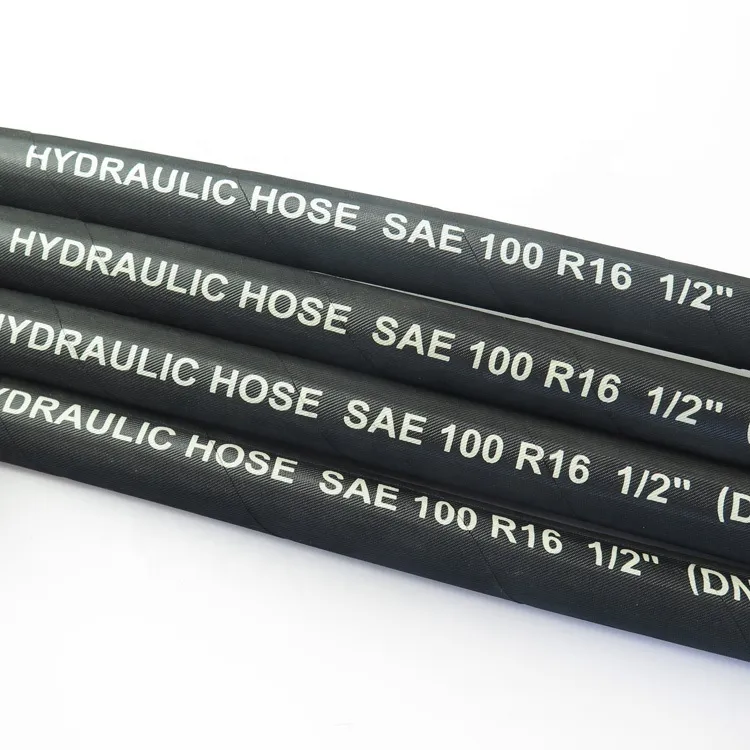
To delve into the utility of high-pressure rubber hose pipes, it is essential to appreciate their construction and the materials that compose them. Crafted from layers of synthetic rubber, these hoses are reinforced with resilient fibers or steel wires, making them apt for high-stress environments. The inner lining is typically smooth and chemically resistant, allowing for seamless flow while preventing corrosion or reactions with diverse substances.
Perhaps the most captivating aspect of these hoses is their adaptability to varying pressure levels, temperature ranges, and environmental conditions—attributes that testify to their reliability and efficiency. This adaptability ensures that industries requiring precise pressure management, such as hydraulic systems in heavy machinery and sophisticated agricultural irrigation systems, find them indispensable.
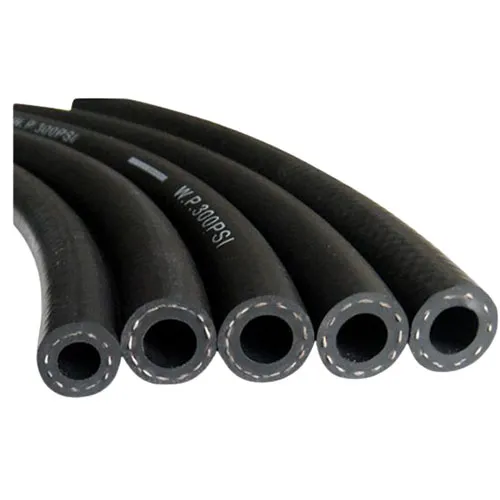
A pertinent example of expertise in action is observing how the automotive industry leverages high-pressure rubber hoses. These components are crucial for conveying fluids such as oil, coolant, and fuel, often under intense temperature and pressure variations. The reliability of these hoses directly impacts vehicle performance and longevity, establishing them as a cornerstone of automotive engineering.
high pressure rubber hose pipe
The authority of high-pressure rubber hose providers is further affirmed through compliance with rigorous international standards, such as the SAE (Society of Automotive Engineers) specifications. This adherence ensures that these hoses meet stringent safety, durability, and performance benchmarks, fostering trust among industry professionals and end-users alike.
Moreover, real-world experience highlights the importance of proper maintenance and inspection protocols to extend the service life of high-pressure rubber hoses. Regular inspections for wear, signs of leakage, or inner tube degradation are critical. An industry practice is to employ predictive maintenance techniques, leveraging technology to foresee potential failures, thus minimizing downtime and enhancing operational efficiency.
When discussing trustworthiness in the context of these hoses, the emphasis shifts towards transparency in manufacturing processes and material sourcing. Reputable manufacturers often provide detailed insights into their quality control methods and the sourcing of raw materials, offering assurance regarding product reliability and environmental responsibility.
In sum, high-pressure rubber hose pipes stand as a testament to engineering innovation, offering unmatched solutions for fluid and gas transfer needs across varied domains. Their composition and construction underscore significant expertise, while adherence to global standards and vigilant maintenance and manufacturing practices bolster their authority and trustworthiness. By understanding these elements, industries can optimize their operations, ensuring safety and efficiency with each hose deployment.