In the world of industrial applications and demanding environments, the heat resistant tube rubber hose stands out as a critical component, designed to withstand extreme temperatures and punitive conditions. For industries ranging from automotive to chemical processing, these hoses are not just ancillary components; they are indispensable. Their robust nature ensures longevity and reliability, making them a preferred choice among engineers and procurement specialists alike.
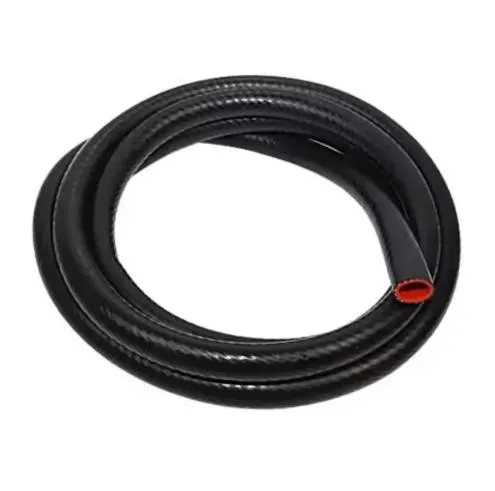
Heat resistant rubber hoses are constructed using advanced material science. Typically crafted from high-grade synthetic rubber compounds such as EPDM (ethylene propylene diene monomer) or silicone, these hoses demonstrate exceptional durability. EPDM is particularly renowned for its heat resistance, flexibility, and resilience against environmental factors, offering excellent protection against the ozone, UV rays, and general weathering. Silicone, on the other hand, can withstand even higher temperatures and provides exceptional fire resistance, making it an ideal choice for high-risk settings where safety is paramount.
The performance of these hoses in high-temperature applications—often exceeding 200 degrees Celsius—is a testament to their design and construction. Industries rely on these hoses to transport fluids and gases without degrading, thus maintaining the integrity of the operation and safeguarding machinery from potential damage. In automotive applications, for example, heat resistant hoses are used in cooling and heating systems, where they efficiently handle coolant transfer even under high pressure and temperature conditions.
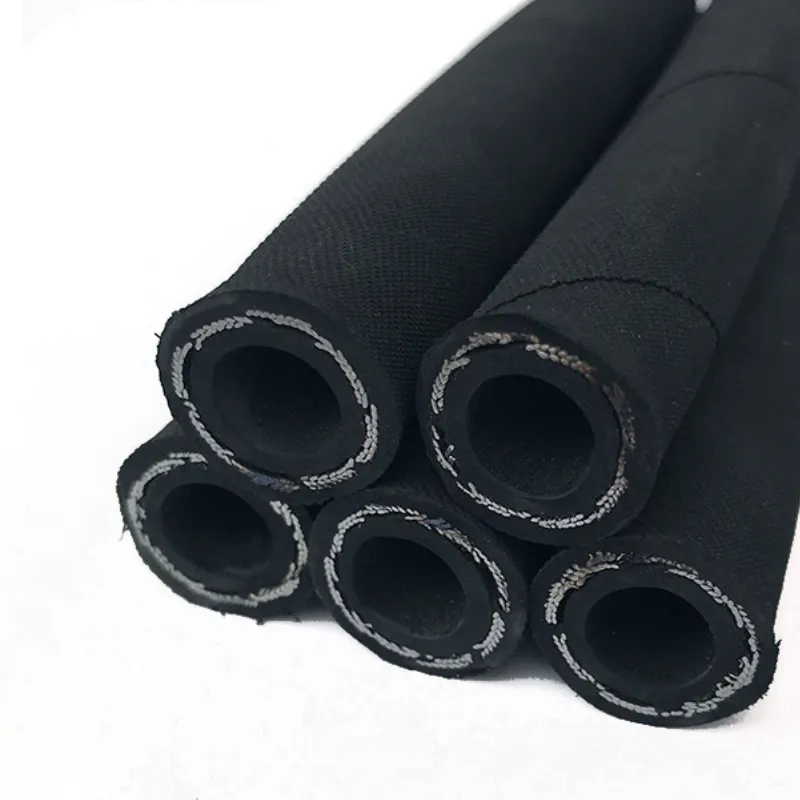
Expertise in selecting the right heat resistant rubber hose is crucial. Engineers and technicians must consider factors such as pressure capacity, flexibility, outer coating resistance, and compliance with industry standards. The application’s specific requirements will dictate the choice of hose type. For instance, in chemical plants, where exposure to aggressive chemicals is a risk, the chemical resistance of the rubber compound becomes an essential parameter.
heat resistant tube rubber hose
Authoritativeness in this domain emanates from adherence to rigorous testing and certification standards. Certified manufacturers ensure that every hose undergoes stringent quality checks according to ISO or ASTM standards, verifying not only heat resistance but also tensile strength and overall durability. These certifications serve as written guarantees of performance, earning the trust of users who require unwavering assurance of operational continuity.
Trustworthiness in the utilization of heat resistant tube rubber hoses is amplified through case studies and user testimonials. Many industry experts share success stories where the implementation of high-grade hoses led to enhanced performance and reduced downtime. In power plants, for example, the proper installation of these hoses can significantly enhance efficiency by preventing overheating issues, a common cause of operational disruptions.
The continuous innovation in material science drives the evolution of heat resistant hoses. This perpetual advancement ensures these components remain at the forefront of industrial applications, providing solutions that not only meet present demands but also anticipate future challenges. As global industries push the boundaries of technology and performance, the impeccable role of heat resistant rubber hoses as guardians of safety and efficiency remains indisputable.
In conclusion, the role of heat resistant tube rubber hoses in industrial environments cannot be understated. Their integration into complex systems ensures operational efficiency, safety, and reliability across various sectors. By combining robust material science with meticulous engineering practices and stringent quality control, they continue to be an essential component in advancing industrial capabilities.