In the realm of heavy industry, the unsung hero consistently linking processes together is often a high-pressure industrial hose. These robust hoses function as vital arteries in a vast range of industrial applications from chemical processing plants and offshore drilling rigs to construction sites and manufacturing facilities. As a seasoned expert in industrial components, I have been deeply involved in assessing the quality, durability, and efficiency of these indispensable tools, providing insights that underscore their pivotal role in ensuring seamless operations across industries.
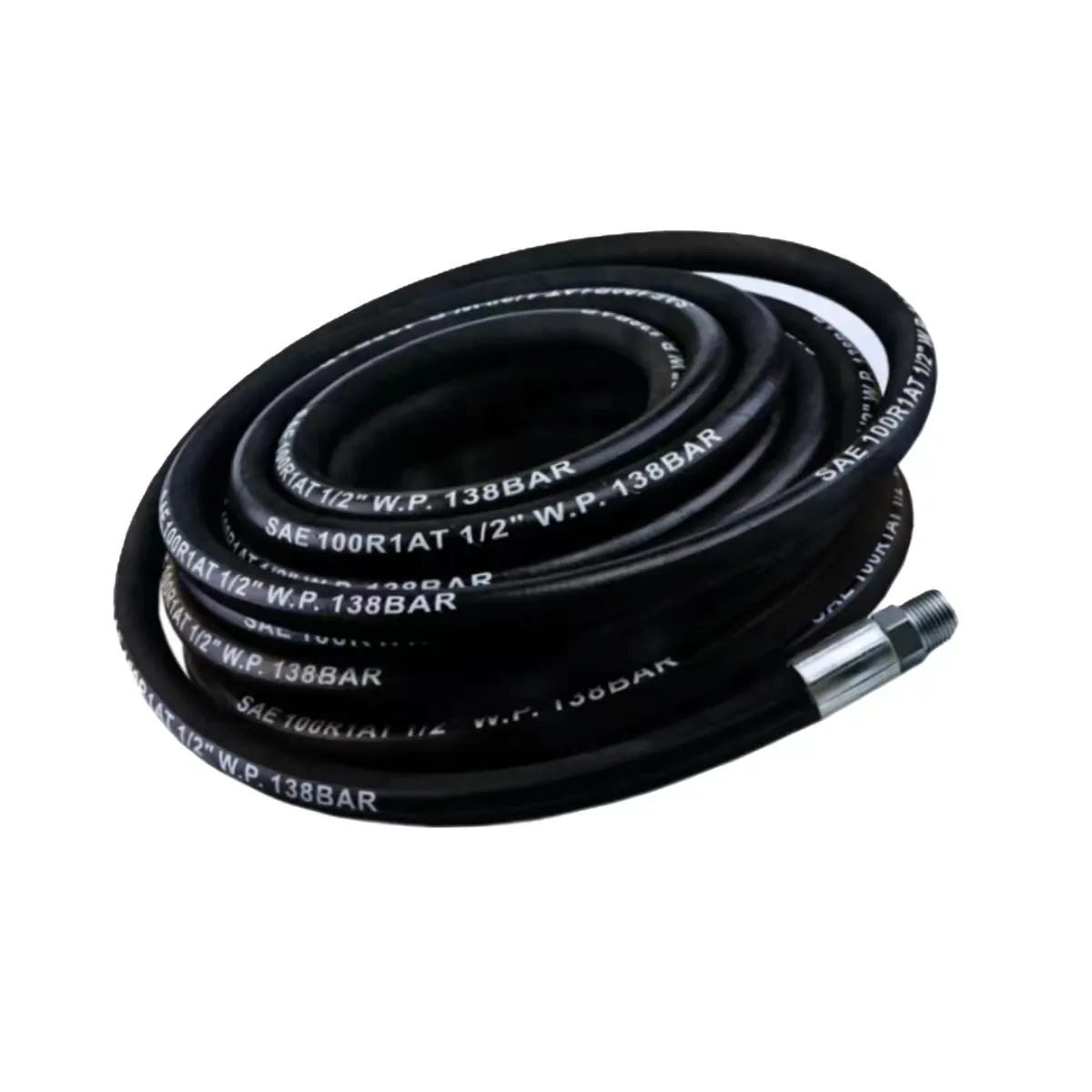
When discussing high-pressure industrial hoses, their paramount importance begins with composition and design. Crafted from a synthesis of reinforced rubber, thermoplastic materials, or high-strength polymers, these hoses must withstand not only high pressures but also extreme temperatures, abrasive conditions, and corrosive substances. The manufacturing processes—often involving multi-layered reinforcements—are critical in achieving the desired strength and flexibility, ensuring that the hoses accommodate rigorous operational demands without compromising safety and reliability.
One pertinent case study involves replacing standard hoses with high-pressure variants in a chemical plant. Despite the initial investment being considerable, the turnaround in operational efficiency was impressive. Low-quality hoses frequently ruptured under high pressure, leading to downtime and potential hazards. The introduction of high-pressure industrial hoses reduced maintenance needs and improved safety measures, illustrating a long-term value that far outweighed the initial costs.
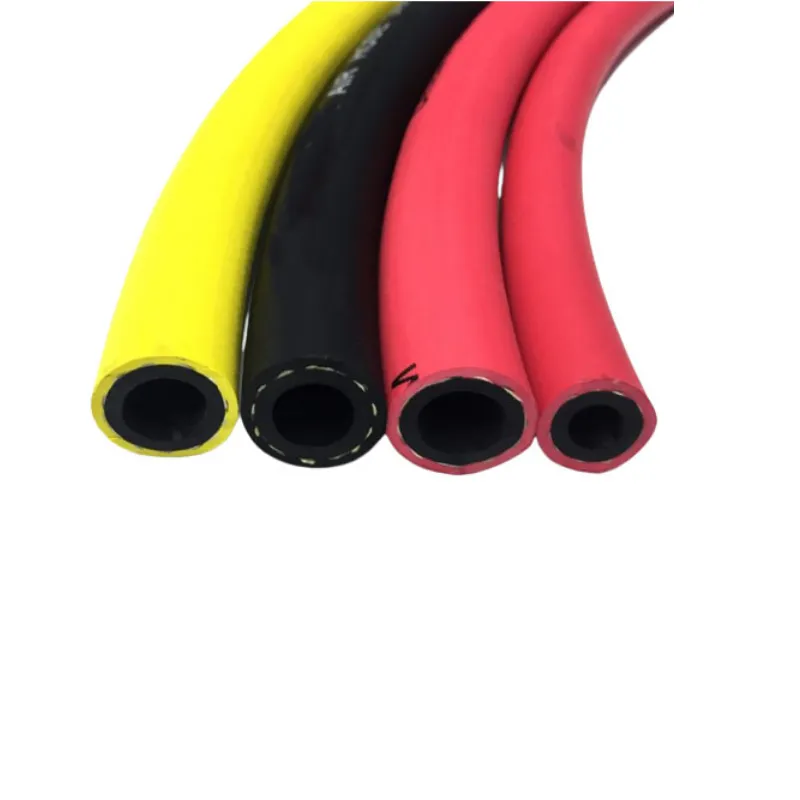
In-depth knowledge of pressure ratings is vital for selecting the correct high-pressure industrial hose. Misjudging these ratings could lead to catastrophic failures. Each hose has its pressure capacity, usually expressed in PSI (pounds per square inch), and understanding this capacity vis-à-vis the system’s operation parameters is essential. For engineers, understanding the intricacies of working pressures and burst pressures ensures sustainable and risk-free integration of these hoses into their systems.
high pressure industrial hose
An oft-overlooked aspect is the fittings and couplings employed with these hoses. Compatibility and quality of these components can significantly affect overall system performance. Poorly-fitted or low-grade fittings can cause leaks and pressure build-ups, which are not just inefficient but potentially dangerous. It's advisable to source these fittings from reputable manufacturers and ensure they comply with industry standards, thus fortifying the integrity and performance of the high-pressure system as a whole.
Trust and credibility in industrial components such as these are cemented through certifications and compliance with international safety standards like ISO 6803 and SAE J343. These standards ensure that the hoses have been rigorously tested for performance under specified conditions, and compliance indicates a manufacturer’s commitment to quality and safety. For procurement specialists, verifying these certifications can be a decisive factor, assuring stakeholders of the product's reliability and conformance to global safety benchmarks.
Understanding proper maintenance routines furthers the lifecycle and efficiency of high-pressure industrial hoses. Regular inspections for wear and tear, adherence to recommended pressure limits, and preventive replacement schedules should be integral components of any maintenance strategy. Real-life observations have shown that overlooked routine checks, particularly in high-stakes environments like oil rigs and chemical plants, could lead to unexpected failures, project delays, and costly repairs.
In conclusion, high-pressure industrial hoses are indispensable to contemporary industrial operations, bridging the gap between robust performance demands and innovative material sciences. They demonstrate a complex convergence of engineering, safety, and economics, continually evolving to meet new industrial challenges. For industry professionals, the roles of understanding specifications, ensuring quality fittings, verifying industry standards, and maintaining rigorous inspection routines cannot be understated. Investment in quality high-pressure hoses yields dividends in terms of enhanced safety, efficiency, and peace of mind, affirming their position as critical components in the industrial landscape.