Fluid power hose assemblies are crucial components in numerous industrial applications, renowned for their ability to effectively convey hydraulic fluids under high-pressure conditions. The performance and reliability of these assemblies directly impact the efficiency and safety of hydraulic systems, making their selection and maintenance critical.
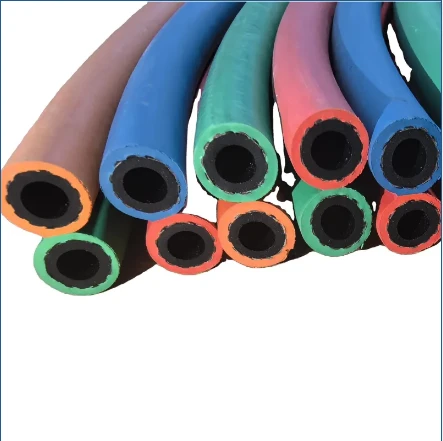
Fluid power hose assemblies consist of a flexible tube, reinforcement layers, and connectors. The intricate design must account for various factors, including the type of fluid being transferred, operating pressure, temperature conditions, and environmental influences. Expertise in fluid dynamics and material science is essential to ensure these assemblies function optimally and safely.
Understanding the types of hoses is fundamental for selecting the right one for your application. Hydraulic hoses, thermoplastic hoses, PTFE hoses, and metal hoses each offer distinct advantages and limitations. Hydraulic hoses, typically made from synthetic rubber, are highly flexible and capable of withstanding high pressures. Thermoplastic hoses are ideal for applications requiring a tighter bend radius and are resistant to degradation from UV exposure. PTFE hoses can handle elevated temperatures and harsh chemicals, while metal hoses, though less flexible, provide unmatched durability and pressure resistance.
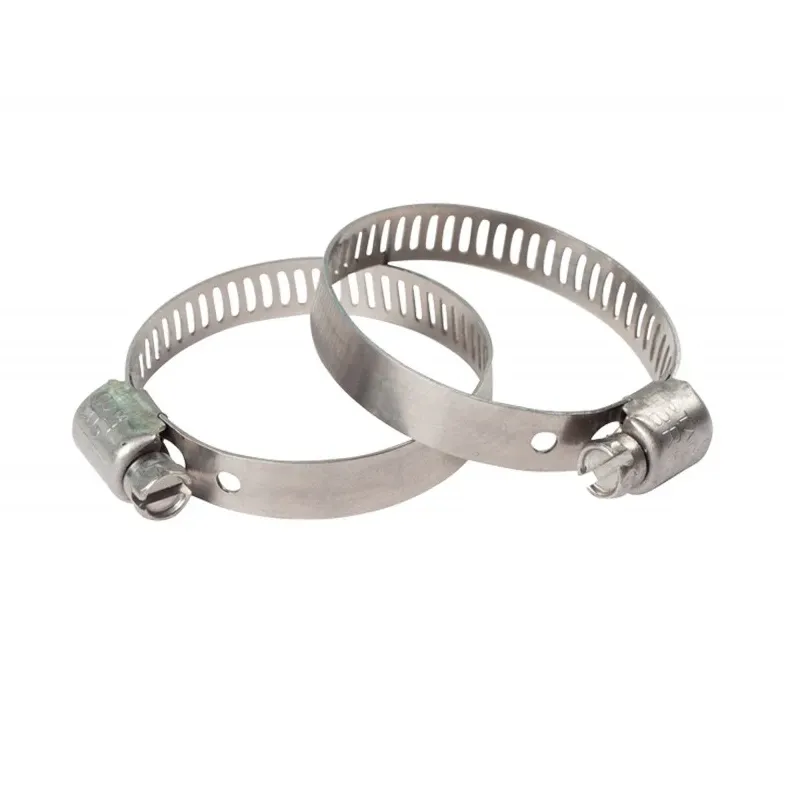
Experts recommend a thorough assessment of the application to determine the appropriate assembly. Analyzing the pressure range is paramount since exceeding the hose's capacity can result in catastrophic failures. Similarly, temperature compatibility must be evaluated, as excessive heat can reduce a hose's lifespan or cause materials to break down. Additionally, consider the chemical compatibility between the hose materials and the fluids conveyed to prevent degradation.
Manufacturers often provide detailed specifications and technical data sheets which outline the hose's operating limits. These documents are invaluable resources; however, consulting experienced professionals brings a level of assurance and insight that goes beyond generic guidelines. Professionals are equipped to offer bespoke solutions tailored to unique operational environments, significantly enhancing performance and longevity.
The connectors or fittings are another critical component, as they secure the hose assembly within the hydraulic system. Improperly installed or selected fittings can lead to leakage or disconnections under pressure, posing serious safety hazards. Choosing fittings made from durable materials, with proper sealing methods like O-rings or taper threads, ensures a secure and leak-free operation.
fluid power hose assembly
Maintenance of fluid power hose assemblies is equally important as selecting the right components. Regular inspections for signs of wear, such as cracks, abrasions, or bulges, can preempt failures. Replacement of worn hoses should follow manufacturer guidelines and incorporate new technologies when available, which often offer improved performance and safety standards.
Moreover, authoritativeness in the industry can be bolstered by partnering with established suppliers known for their high-quality products and commitment to innovation. This collaboration can enhance the reputational profile of a business, fostering trust with clients who demand verified quality and reliability.
Documented evidence of case studies or testimonials from industries that successfully utilize specific hose assemblies can serve as persuasive evidence of a product's efficacy. These real-world examples provide credence to manufacturer claims and offer valuable insights into the practical application of assemblies under varying conditions.
Investing in employee training can reinforce trustworthiness. Educating staff about proper assembly and installation techniques, as well as safety protocols, minimizes risks and elevates operational standards. In-house experts capable of addressing technical issues or conducting routine maintenance offer an additional layer of quality assurance.
Incorporating advanced technologies, like smart hose assemblies equipped with sensors for monitoring pressure and predicting failures, demonstrates a forward-thinking approach that aligns with modern Industry 4.0 initiatives. Such innovations not only improve efficiency but also proactively enhance system reliability.
Fluid power hose assemblies are indispensable, and their proper management is paramount to industrial success. By embracing a comprehensive approach that values expertise, authority, and trust, businesses can ensure the seamless and secure operation of their hydraulic systems, delivering optimal outcomes that meet and exceed industry standards.