When considering the core components of heavy machinery, efficiency, and safety often lead the list of priorities. At the heart of many such systems is the humble hydraulic hose, particularly the 12 hydraulic hose, which commands significant respect in industrial applications due to its robustness and precision in operation. Through my specialized experience, I have gained insights into the complexities and critical nature of these components, making them deserving of the spotlight for anyone involved in hydraulic systems.
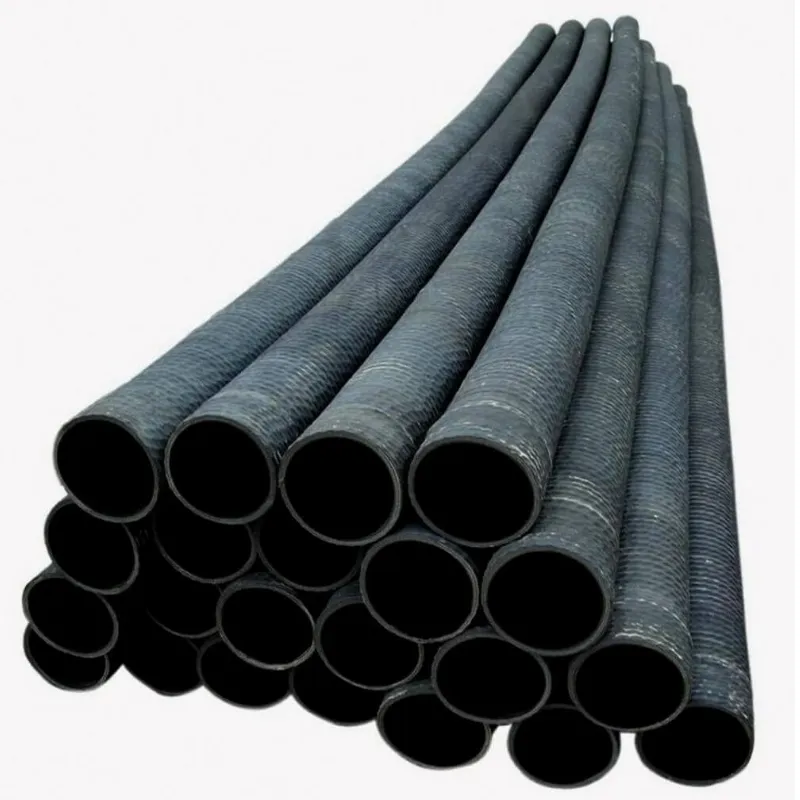
The 12 hydraulic hose stands out primarily for its adaptability and strength. Engineered to perform under extreme pressures, these hoses are essential for transferring hydraulic fluid between different components, often at pressures reaching or exceeding 4,000 PSI. Their structural integrity is critical, as any malfunction can lead to catastrophic failures, endangering life and equipment. This makes choosing the right hose not just a matter of performance but also of safety and longevity of the machinery.
The construction of a 12 hydraulic hose is where its expertise lies. Most reputable manufacturers layer synthetic rubber, steel wire, or textile material, creating a robust barrier against abrasive environments, extreme temperatures, and chemical exposure. Such construction ensures a longer lifespan and reduces the overall maintenance costs of hydraulic systems. Given the varied industrial applications—from construction machinery to agricultural equipment—a 12 hydraulic hose must deliver consistent performance across different settings, a feat it achieves through meticulous design and rigorous testing.
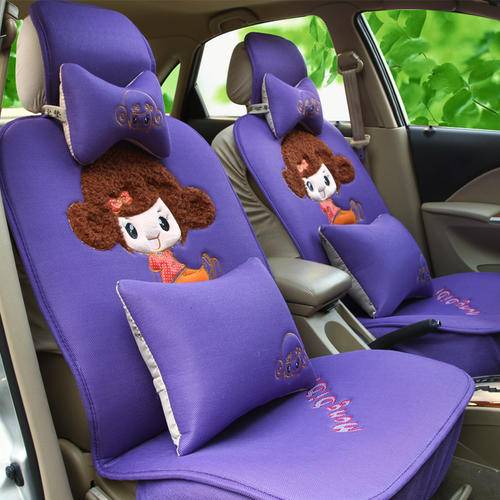
Within industrial settings, one quickly realizes the importance of choosing a hose based not only on pressure capacity but also on specific application needs. Here, expert knowledge comes into play. Depending on the type of hydraulic fluid and temperature ranges, different inner tube materials might be required. For instance, in environments where fluid compatibility and heat resistance are paramount, hoses with PTFE or thermoplastic linings are often preferred. Such decisions underscore the expertise required in effectively matching a hose to its operational environment for optimal performance and safety.
Authoritativeness is established in the industry not just by knowing the technical specifications but by adhering to global manufacturing standards. Many highly regarded 12 hydraulic hoses are manufactured according to standards set by the International Organization for Standardization (ISO) and the Society of Automotive Engineers (SAE). ISO 18752 and SAE 100R12, for example, are critical guidelines ensuring the material quality and performance benchmarks are consistently met. These standards provide a basis on which suppliers and end-users can trust the hose's performance, knowing it has endured rigorous testing and quality assurance processes.
12 hydraulic hose
Incorporating trustworthy suppliers into your selection process is equally important. Reputable manufacturers often engage in direct communication with clients, offering product demonstrations, thorough documentation, and continuous support to ensure that the hose solutions provided are optimal for their applications. This level of customer service builds trust, ensuring confidence in the product's capabilities, and illustrates a commitment to maintaining high safety and performance standards.
Furthermore, incorporating the latest innovations in hydraulic hose technology can lead to improved operational efficiency. For example, some cutting-edge hoses incorporate sensor technology to provide real-time data on pressure, temperature, and flow rates. This facilitates predictive maintenance, reducing downtime and the risks associated with unexpected hose failures. Investing in such advancements demonstrates a forward-thinking approach, positioning businesses at the leading edge of technological improvements.
Maintaining and inspecting hydraulic systems is crucial for preserving their integrity. Regular audits and proactive maintenance checks can prevent wear-induced failures before they lead to system breakdowns. Implementing a routine that includes visual inspections, pressure validation, and leak identifications, ideally automated via sensor integrations, can significantly extend the lifespan of your hydraulic hoses.
Overall, understanding the multifaceted nature of 12 hydraulic hoses is essential for maximizing their utility and ensuring the safety of hydraulic systems. By relying on a wealth of experience, professional expertise, authoritative manufacturing standards, and strengthening trust through reliable suppliers, industries can harness the full potential of these vital components, assuring performance excellence and safety across the board.