The evolution of fuel rubber hoses is a fascinating testament to decades of material science advancements, underscoring their role as indispensable components in both automotive and industrial applications. These specialized hoses serve as vital conduits, ensuring the safe and efficient transport of fuel, and it's imperative to understand their composition and selection criteria to make informed purchasing decisions.
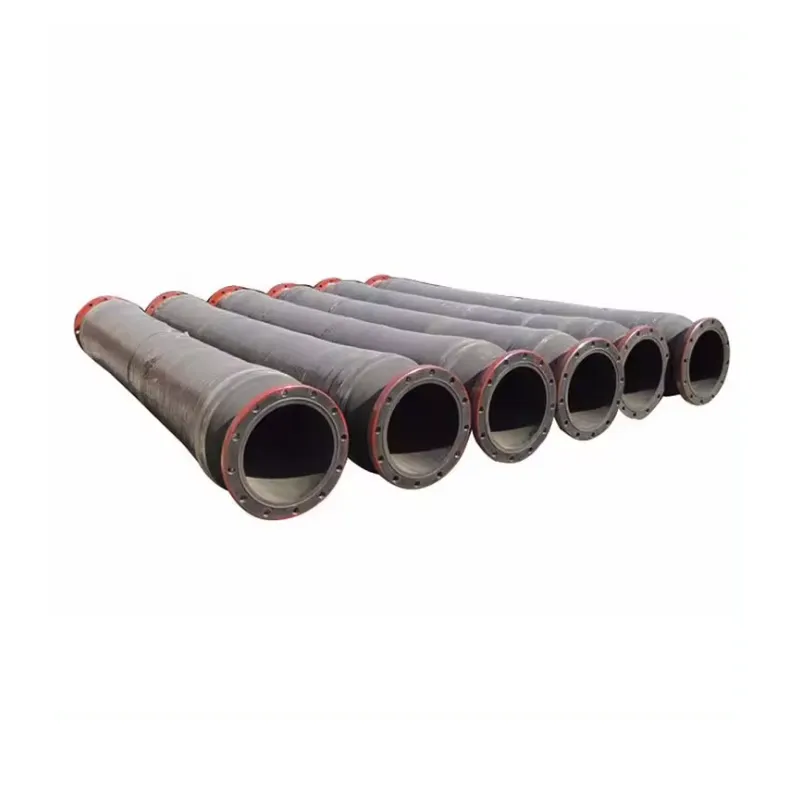
When discussing fuel rubber hoses, it’s crucial to appreciate the intricate balance between flexibility and durability. These hoses are typically constructed using a combination of synthetic rubber and high-strength textile fibers. The synthetic rubber provides the necessary elasticity to absorb vibrations and fuel pressure fluctuations, while the fiber reinforcement enhances the hose’s ability to withstand pressure and resist kinking. This construction ensures that the hoses can function optimally under the challenging conditions present in automotive engines and industrial machinery.
A key factor in evaluating fuel rubber hoses is their resistance to chemical degradation. Fuel, comprising a mix of hydrocarbons and additives, can be corrosively potent. The material of the hose must offer exceptional resistance to degradation, preventing leaks and maintaining safety. High-quality hoses are often lined with fluoropolymer or nitrile rubber, known for their superior resistance to fuel and oil. These materials ensure that the hose does not crack or swell over time, providing a long-lasting solution.
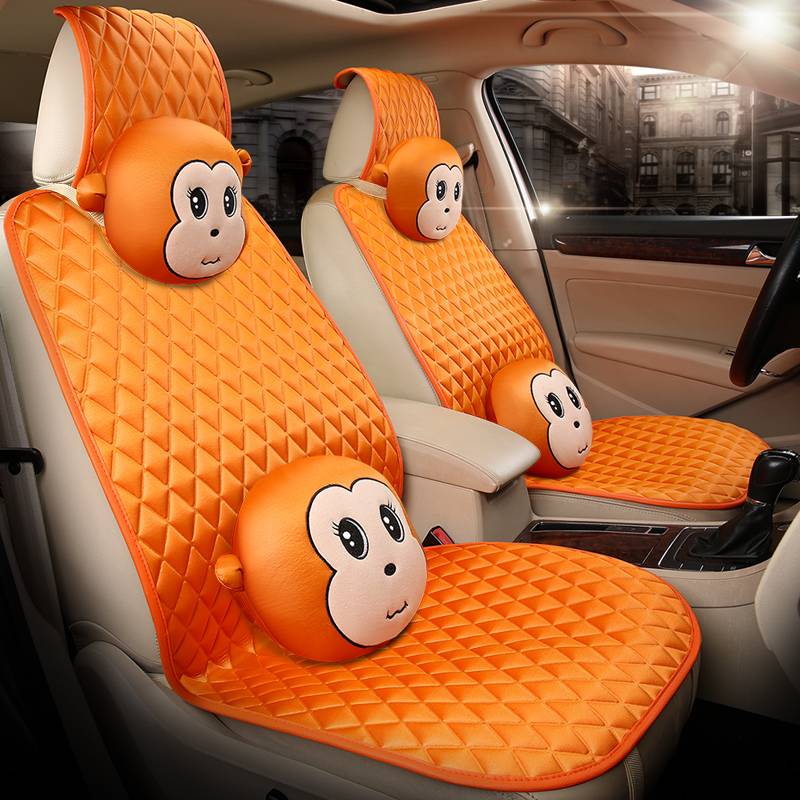
Temperature resistance is another critical consideration. Hoses operating in engines are exposed to a wide temperature range, and failure to withstand these extremes could result in catastrophic fuel leaks. Advanced fuel rubber hoses boast a wide temperature tolerance, often ranging from sub-zero to over 100 degrees Celsius. This makes them ideal for varied climatic conditions and diverse engine co-operations, whether it's the icy tundra or a scorching desert.
In terms of industry standards, it's essential to consider the certifications associated with fuel rubber hoses. Reputable manufacturers ensure their products meet stringent standards such as SAE J30R7 or J30R9, which stipulate the necessary specifications for fuel hoses, including burst strength and permeability ratings. Selecting hoses that adhere to these standards ensures conformity to safety norms and reliability in performance.
fuel rubber hose
Compatibility is another pivotal factor. Not all fuel rubber hoses are created equal, and selecting a hose appropriate to the type of fuel used is crucial. Gasoline, diesel, biodiesel, and ethanol blends all interact differently with rubber compounds. Understanding the chemical composition of the fuel and selecting a corresponding hose are crucial steps to avoid degradation or premature failure.
Beyond technical specifications, the expertise of seasoned professionals can offer invaluable insights into the performance and longevity of fuel rubber hoses. Mechanics, engineers, and industrial technicians have a keen understanding of these components’ practical applications, ensuring users can select the optimal product for their specific needs. This hands-on experience translates into selecting fuel rubber hoses with the precise diameter, reinforcement braid type, and length, optimizing performance, and extending the longevity of the equipment.
For reliability and peace of mind, sourcing from authoritative brands with a proven track record in manufacturing can’t be overstated. Brands that invest in research, development, and rigorous testing contribute significantly to product trustworthiness. Companies known for high manufacturing standards ensure that every hose is subjected to thorough inspection, thus minimizing the risk of defects.
Ultimately, selecting the right fuel rubber hose is not merely about spending on a component but making an investment that ensures the longevity and safety of vehicles and machinery. With advances in material sciences and manufacturing processes, modern fuel rubber hoses are engineered to deliver unmatched performance and durability, presenting an exemplary blend of reliability and innovation. Making well-informed decisions based on expertise, product-specific parameters, and expert consultations can lead to enhanced operational efficiency and cost savings in the long run.