Conductive rubber hoses are revolutionizing industries where safety and efficiency are of paramount importance. Known for their dual functionality of transferring both materials and electrical signals, these hoses have become essential in environments demanding the highest standards of operational integrity and safety.
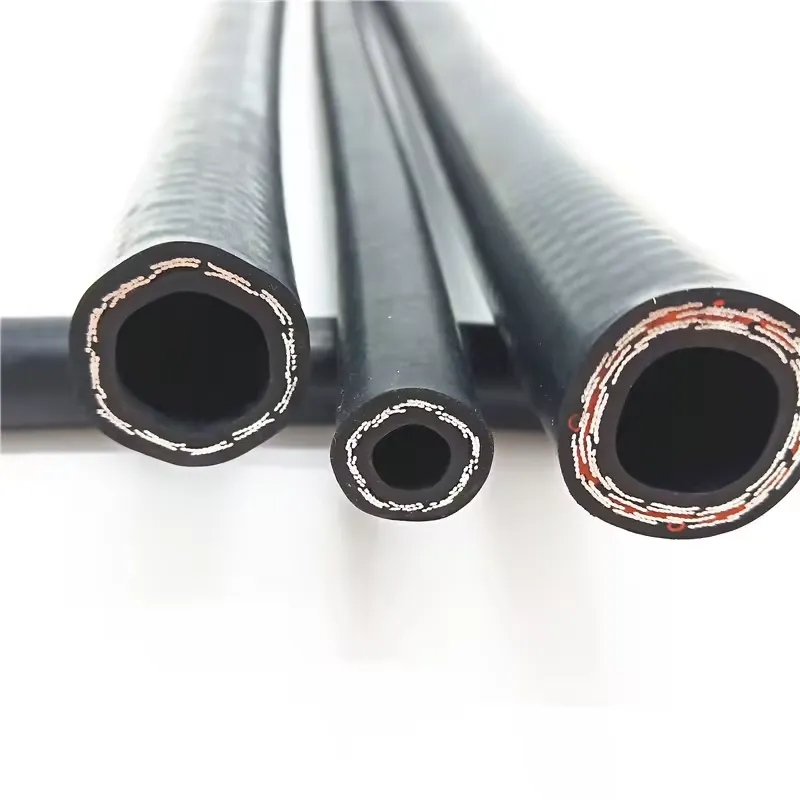
The uniqueness of conductive rubber hoses lies in their design. Unlike conventional hoses, these incorporate conductive materials within their structure, typically employing carbon black or metal fibers. This incorporation transforms the hose into more than just a conduit for materials, enabling it to dissipate static electricity generated during the transportation of flammable or explosive substances. This built-in conductivity mitigates risks of static discharge, which can lead to catastrophic events in sensitive environments like chemical plants, refineries, or areas dealing with combustible dust.
Professionals working in industries that handle volatile substances have increasingly recognized the value offered by conductive rubber hoses. The real-world experiences shared by industry experts highlight several benefits these hoses provide. For instance, in the petroleum industry, engineers have noted the hoses' exceptional ability to maintain safety standards while handling gasoline and other fuels. This safety is achieved without compromising the hoses' flexibility or durability, allowing users to maneuver and implement them in rigorous and demanding operational scenarios.
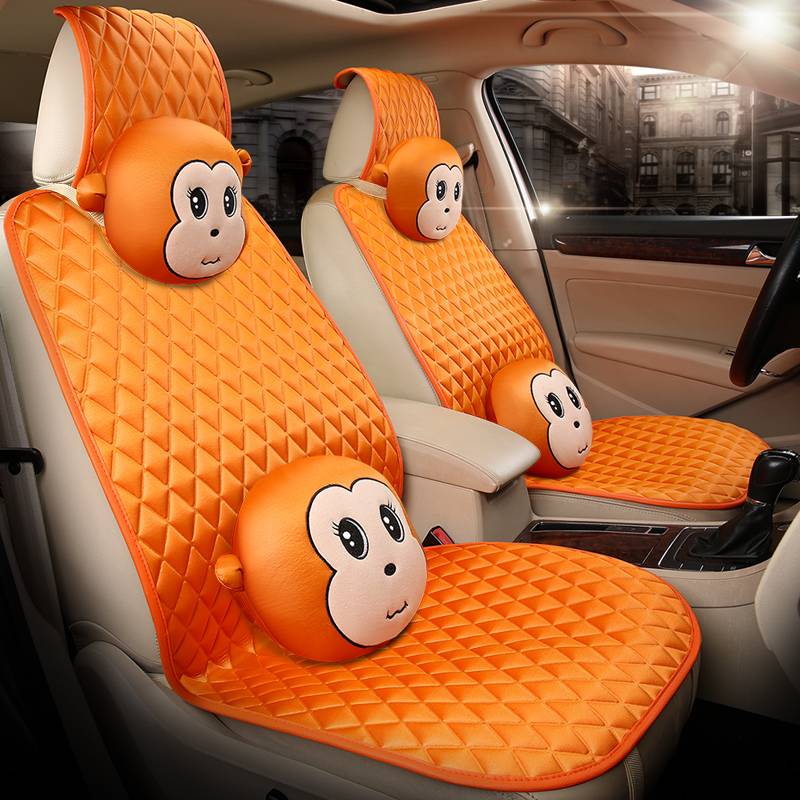
From an expertise standpoint, the development of conductive rubber hoses has been driven by a deep understanding of material science and engineering principles. The integration of conductive properties into elastomers requires precise engineering to maintain the balance between flexibility, conductivity, and mechanical strength. Renowned research and development teams across the globe are continuously innovating the compositions and manufacturing processes. Their work ensures that these hoses not only meet industry standards but exceed them, providing longer service life and enhanced performance.
conductive rubber hose
Trustworthiness is a critical factor when it comes to the implementation of such technology in industrial settings. Manufacturers of conductive rubber hoses adhere to stringent testing protocols, ensuring each product can withstand the harsh environments it might face. This includes extensive testing for abrasion resistance, tensile strength, and electrical conductivity. Compliance with international safety certifications, such as those from the International Electrotechnical Commission (IEC) or Underwriters Laboratories (UL), further reinforces the reliability of these products.
In addition to their application in traditional industries, conductive rubber hoses are finding new applications in emerging fields. The aerospace sector, for example, is exploring their use in aircraft fuel systems to reduce the risk of static discharge, thereby enhancing in-flight safety. Similarly, in the electric vehicle industry, these hoses play a crucial role in the safe transfer of battery fluids, ensuring that no static build-up occurs during charging and discharging cycles.
To achieve optimal SEO results for this topic, focus on targeting keywords that industry professionals might search for, such as safety in fuel transfer, static dissipation in hoses, and conductive hose applications. Additionally, incorporating case studies and testimonials from industry users can enhance the content's authority, providing firsthand insights into the advantages of using conductive rubber hoses.
The ongoing advancements in conductive rubber hose technology underscore their importance across diverse sectors. As industries continue to prioritize safety and efficiency, the demand for these innovative hoses is projected to rise. For businesses looking to stay ahead of the curve, investing in conductive rubber hoses represents a commitment to cutting-edge safety and operational excellence.