Selecting the right chemical rubber hose plays a critical role in a variety of industrial applications. From transporting reactive chemicals to ensuring the safety of operations, the significance of these components cannot be overstated. With a myriad of options available in the market, understanding their features, benefits, and selection criteria is imperative for operational efficiency and safety.
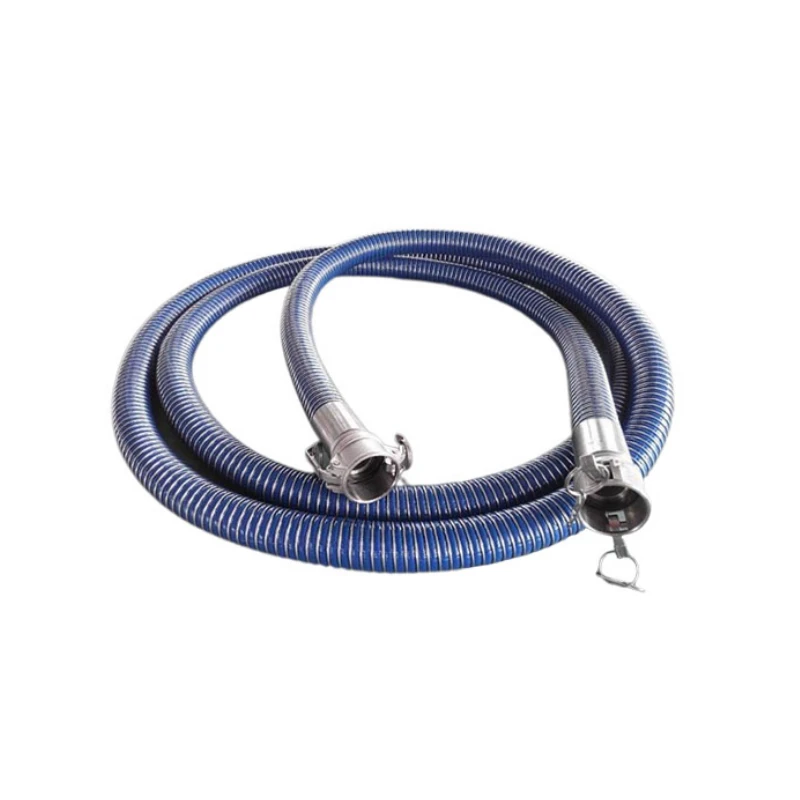
Chemical rubber hoses are engineered to convey a wide range of chemicals under diverse conditions. Their construction typically involves a synthetic rubber tube reinforced by multiple layers of materials like polyester, wire, or nylon, which fortify the hose to withstand high pressures and temperatures. The exterior is often made from neoprene or other durable materials to provide resistance to weather, abrasion, and aging.
The primary consideration in selecting a chemical rubber hose is its compatibility with the intended chemical substances. This ensures that the hose will not degrade, swell, or react with the chemicals it is meant to convey. Reputable manufacturers provide exhaustive compatibility charts and sometimes offer custom hose solutions tailored to specific chemical environments. Industry experts recommend consulting these resources to avoid costly and dangerous hose failures.
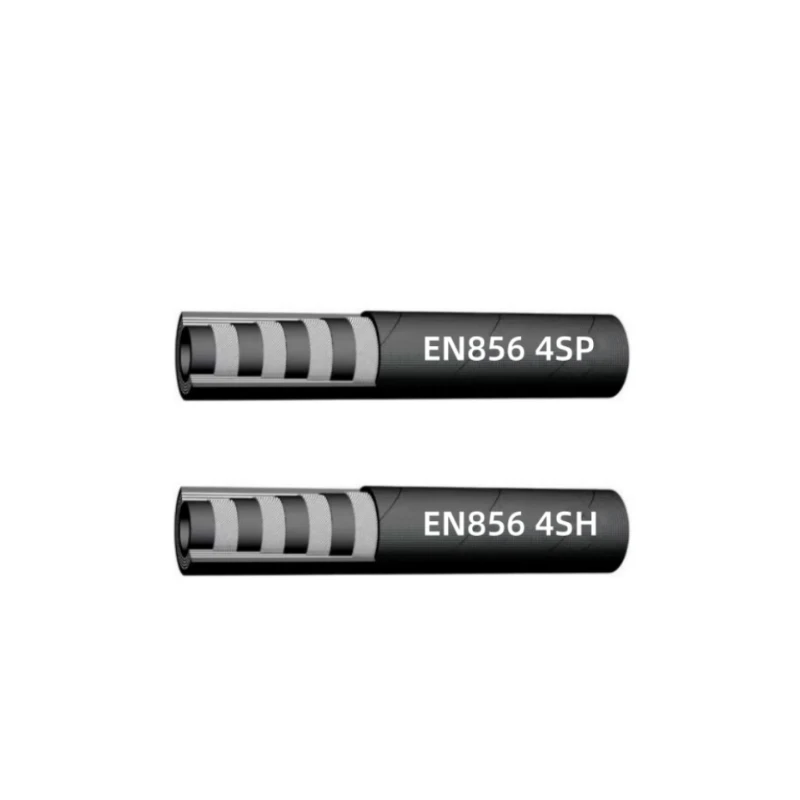
In addition to chemical compatibility, the operating temperature and pressure ratings are crucial specifications to consider. A hose should be capable of functioning reliably within the parameters of the system it serves.
Exceeding these ratings can result in dangerous ruptures or leaks. Consulting with engineers or using predictive models to gauge expected performance under various scenarios can enhance safety and longevity.
Certification and compliance with industry standards (such as ISO, EN, or ANSI) underline the quality and trustworthiness of a chemical rubber hose. These certifications often ensure that a hose has undergone rigorous testing for durability, pressure resistance, and material integrity. This, in turn, provides assurance of the reliability and safety of the hose during its operational lifetime.
chemical rubber hose
Another aspect to consider is the flexibility of the hose, which impacts handling and installation. A more flexible hose allows for easier maneuvering around equipment and obstacles, reducing labor costs and installation time. It also minimizes stress on the hose ends, prolonging the service life.
Proper maintenance of chemical rubber hoses enhances safety and performance. Regular inspections should be scheduled to check for signs of wear, such as cracks, blistering, and abrasion. A maintenance routine may also involve pressure testing and flushing the hose to prevent blockages and buildup of residues, thereby extending its operational life and maintaining safety standards.
Trustworthiness in chemical rubber hose service also involves investing in reliable partnerships. Partnering with established manufacturers or suppliers known for consistent quality and robust customer service can be invaluable. They can provide essential support, from initial product selection to after-sales service, ensuring that users derive maximum value and safety from their investment.
As industries evolve, so do the demands on chemical rubber hoses. Emerging technologies, like reinforced composite materials, enhance hose capability and resilience under extreme conditions. Staying informed about these innovations and integrating them into applications can offer competitive advantages, including improved efficiency and reduced risk.
In conclusion, the expertise involved in choosing the correct chemical rubber hose underscores its vital role in industrial operations. By focusing on compatibility, regulatory compliance, flexibility, and proper maintenance, businesses not only safeguard their operations but also enhance efficiency and value. Engaging with informed, experienced partners also amplifies these benefits, making the right hose choice a central component of operational success.