When it comes to maintaining the efficiency and longevity of any heavy-duty machinery, the importance of a coolant tube cannot be overstated. This seemingly simple component plays a critical role in regulating the temperature, ensuring that engines and other mechanical systems remain functional and safe from overheating. For anyone invested in the industrial sector or automobile maintenance, understanding the intricacies of coolant tubes can spearhead both operational efficiency and cost-effectiveness.
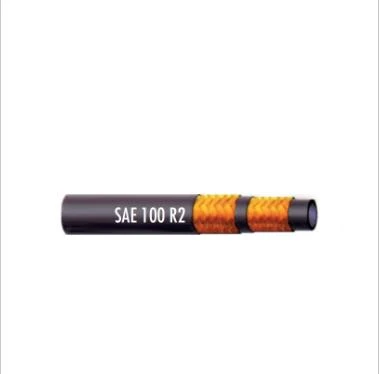
Selecting the right coolant tube is pivotal. Made from a variety of materials such as rubber, silicone, or metal, each type presents its own set of advantages. For instance, rubber tubes offer flexibility and are resistant to extreme temperatures, making them ideal for dynamic environments where extensive movement is expected. Silicone tubes, on the other hand, are revered for their excellent thermal stability, making them suitable for high-temperature applications. Metal tubes boast superior durability and are typically impervious to chemical reactions, thus extending their life span in harsh conditions.
Not only does the material matter, but so does the size and design. Proper sizing ensures that the coolant flows consistently without blockages, leading to optimal heat dissipation. Tubes with advanced internal structures can enhance turbulence, improving the cooling efficiency. Engaging with professionals who have substantial expertise in fluid dynamics can greatly influence the choice of an appropriate design tailored to specific machinery.
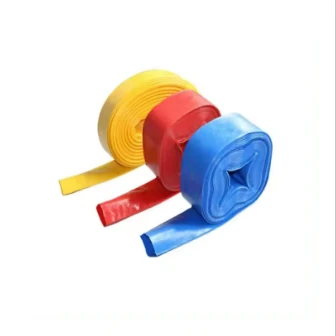
Installing and maintaining a coolant tube requires diligence and expertise. The installation process should be entrusted to skilled technicians who understand the nuances of ensuring air-tight connections and optimal alignment. A poorly installed tube can lead to leaks, reducing efficiency and potentially causing damage. Regular maintenance checks are imperative; inspecting for wear signs such as cracks, hard spots, or unusual bulges can preemptively address issues before they escalate.
coolant tube
Moreover, a coolant’s composition flowing through these tubes can affect both the tube’s longevity and the system's overall performance.
It's advisable to use a high-quality coolant tailored to the specific requirements of the machinery. Coolants that are contaminated or mixed with incompatible substances can corrode or degrade tubes, leading to premature failures.
In-depth knowledge about the evolving technologies in the production of coolant tubes enhances one’s expertise. Innovations like reinforced layers and temperature-resistant coatings have significantly reduced maintenance needs while boosting efficiency. Industry leaders and researchers consistently advocate for staying updated with the latest advancements to ensure optimal machinery performance.
Trustworthy brands in the market today offer extensive warranties and customer support, establishing their authority in the industry. Choosing a reputable brand guarantees that the product has been subjected to rigorous testing, aligning with international standards of quality and safety.
A decision to invest in high-quality coolant tubes reflects a commitment to excellence and reliability. Understanding the nuances involved in the selection, installation, and maintenance of coolant tubes not only safeguards machinery but also quenches an insatiable thirst for knowledge and excellence in mechanical engineering. A well-maintained coolant system is indeed the unsung hero of any efficient machine, harmonizing functionality with longevity in the ever-demanding industrial landscape.