Corrugated rubber hoses play a crucial role in a variety of industrial applications due to their flexibility, durability, and ability to withstand harsh environments. Understanding the intricacies of these hoses can significantly enhance their utility and longevity, offering valuable insights for users ranging from field technicians to product managers.
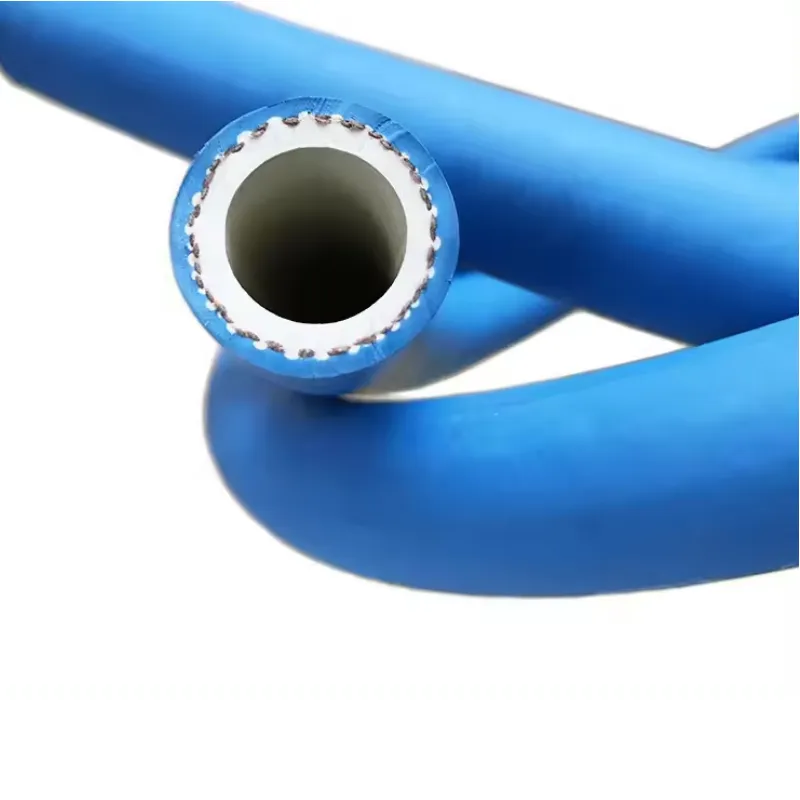
Corrugated rubber hoses are characterized by their unique construction, featuring ridges and valleys that give them the flexibility required in dynamic environments. This design allows them to bend and flex without compromising structural integrity, making them ideal for situations where hoses need to navigate tight spaces or frequently move.
Expert users often choose corrugated rubber hoses for their remarkable resistance to detrimental conditions such as abrasion, chemicals, and temperature extremes. These properties make them particularly suitable for use in industries like automotive, marine, oil and gas, and manufacturing. For instance, in automotive applications, corrugated rubber hoses effectively manage vibration, direct fluids, and handle ducting tasks around complex engine parts.
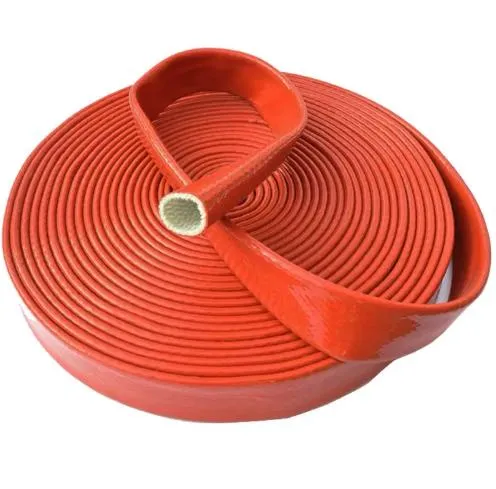
To ensure optimal performance, it's essential to select a corrugated rubber hose that matches the specific requirements of the intended application. Key factors to consider include the operating temperature range, pressure conditions, and chemical compatibility.
Corrugated rubber hoses are available in different composite materials, each designed to meet unique operational demands.
One of the primary components of these hoses is the rubber material itself. This can include natural rubber for its elasticity, EPDM for excellent heat and weather resistance, or nitrile for superior oil resistance. Selecting the right type of rubber based on chemical and thermal interaction is paramount.
Field experts also highlight that the quality of the reinforcement layers within the hose is critical. These layers, often made of synthetic fibers or steel wire, provide the necessary strength to withstand internal and external pressures while maintaining flexibility. The choice of reinforcement depends on the pressure rating and the physical forces the hose must endure.
Trustworthy manufacturers clearly label their products, providing detailed specifications and compliance with international standards like ISO or SAE. This transparency ensures that the hose's performance can be trusted and is backed by rigorous testing. Choosing a reputable supplier is instrumental in guaranteeing the reliability and safety of corrugated rubber hoses.
corrugated rubber hose
The complexity of corrugated rubber hoses means that even the most seasoned experts must approach maintenance with a detailed understanding. Regular inspections can preemptively identify wear and fatigue, preventing failures that could lead to costly downtime. Key inspection points include checking for surface abrasions, leaks, kinks, and ensuring that fittings are secure and corrosion-free.
Furthermore, correct installation practices contribute significantly to the hose’s lifespan. Installation experts recommend that hoses be installed with the appropriate minimum bend radius as specified by the manufacturer to prevent undue stress and potential damage over time. It is equally important to ensure that hose assemblies are correctly aligned with the associated equipment to avoid mechanical strain.
Educating teams and operators on these nuanced practices helps build authority in managing corrugated rubber hoses efficiently. This level of expertise not only enhances productivity but also ensures safety in the workplace by mitigating risks associated with hose failures.
Advanced users can further refine their application strategies by leveraging modern technologies such as Computer-Aided Design (CAD) to simulate installations and anticipate operational loads. These simulations offer an authoritative foundation for making informed decisions about hose environments and configurations.
The industry continues to innovate, and the future of corrugated rubber hoses may include advancements like smart hoses with embedded sensors for real-time monitoring of parameters like temperature and pressure. Such innovations can significantly improve predictability and control, facilitating proactive maintenance and extending hose life.
In conclusion, corrugated rubber hoses serve as vital components in various industries, enabled by their design flexibility and robust material composition. By understanding the elements of material selection, adherence to manufacturing standards, and maintenance protocols, professionals can optimize the use of these hoses, ensuring reliability and safety across applications. The cultivation of a deep understanding of this product type is invaluable, promising long-term savings and operational efficiency for businesses that rely on this indispensable technology.