In the realm of industrial applications, heat resistant rubber hoses are indispensable tools that ensure the safe and efficient transfer of high-temperature fluids. These hoses are designed with precision to withstand extreme temperatures, maintaining both functionality and durability in the most demanding conditions. Understanding the nuances of these products can significantly enhance their application and effectiveness in various industries.
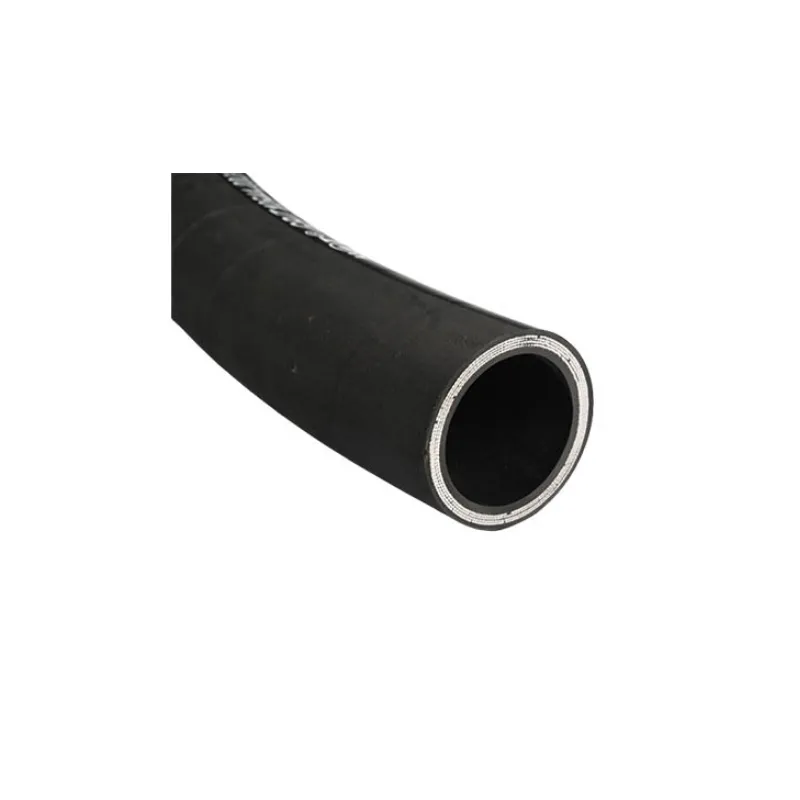
Heat resistant rubber hoses are primarily constructed from high-grade materials like silicone, EPDM (ethylene propylene diene monomer), and Viton. These materials offer unique properties that contribute to the hose's heat resilience. For instance, silicone hoses are renowned for their flexibility and ability to withstand continuous temperatures ranging from -60°C to 220°C. In contrast, EPDM hoses can resist temperatures up to 150°C while also providing excellent resistance to weathering and ozone. Viton, on the other hand, provides exceptional chemical resistance along with heat tolerance up to 204°C, making it suitable for more specialized applications.
Industries such as automotive, aerospace, and manufacturing rely heavily on heat resistant rubber hoses for tasks ranging from coolant transfers to the transportation of fuel and hydraulic fluids. The automotive sector, for example, utilizes these hoses to manage under-the-hood temperatures and optimize engine performance. By using hoses made from materials that can tolerate elevated temperatures, automotive engineers can prevent heat damage, reduce the risk of accidents, and extend the lifespan of vehicle components.
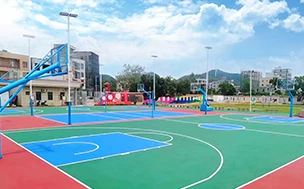
In aerospace applications, heat resistant hoses are crucial for ensuring the safety and performance of aircraft systems. They are often used in fuel lines and hydraulic systems where they must operate under extreme conditions, including rapid pressure changes and high altitudes. The robust nature of these hoses allows them to perform reliably without degradation, which is vital for maintaining the integrity of aerospace operations.
Another significant application of heat resistant rubber hoses is in industrial manufacturing processes. In facilities where machinery generates significant heat, such as plastic molding or metal fabrication, these hoses are deployed to transport steam, hot oils, and other thermal fluids. Their ability to maintain flexibility and strength under high temperatures prevents costly downtime and equipment damage, thereby enhancing production efficiency.
heat resistant rubber hose
The expertise involved in manufacturing heat resistant rubber hoses is of paramount importance. Manufacturers must adhere to stringent quality and safety standards to ensure their products meet industry-specific requirements. This involves rigorous testing processes to evaluate the hose’s temperature tolerance, pressure handling, and chemical resistance. Such comprehensive testing assures users of the hose's reliability and longevity, thereby establishing trust in its performance.
Authoritativeness in the heat resistant rubber hose market often derives from continuous innovation and a deep understanding of material science. Manufacturers investing in research and development can introduce novel compounds and reinforcement techniques, which can improve hose performance significantly. For instance, advances in nanotechnology have led to the development of nanocomposite materials that enhance the thermal properties of rubber hoses, offering better performance at lower costs.
Trustworthiness in choosing a heat resistant rubber hose supplier is crucial for end-users. A reputable supplier will not only provide high-quality products but also offer exceptional customer service, technical support, and after-sales services. Ensuring a direct line of communication between the manufacturer and the client helps in customizing solutions that meet specific operational needs, thereby cultivating a reliable partnership.
In conclusion, heat resistant rubber hoses are critical components across various industries. Their ability to function under extreme temperatures and conditions is a testament to the meticulous design and manufacturing processes underpinning their production. As industries continue to evolve, the role of heat resistant hoses will undoubtedly expand, necessitating ongoing innovation and adaptation to meet new challenges. By prioritizing factors such as material selection, manufacturing expertise, and supplier reputation, businesses can fully leverage the capabilities of these essential tools, driving both safety and efficiency.