Heat-resistant tubing plays a pivotal role in numerous industrial applications, offering a critical solution where extreme temperatures are a concern. Drawing from years of field experience and deep industry expertise, this article delves into various aspects of heat-resistant tubing, providing insights that are both authoritative and trustworthy for anyone considering implementing this solution.
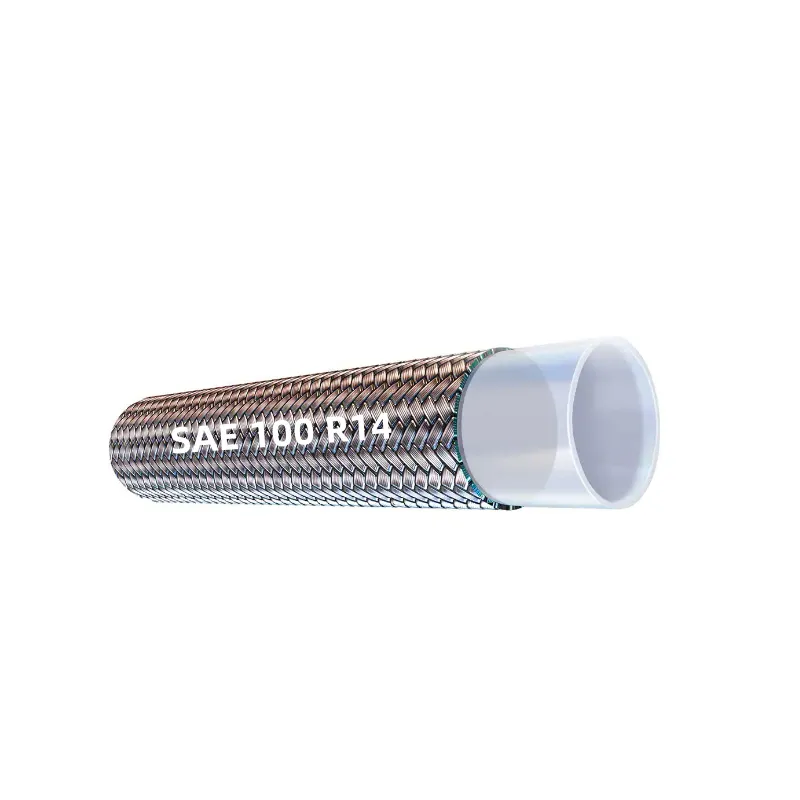
In numerous sectors, from manufacturing and automotive to aerospace and electronics, products must endure and operate efficiently in high-temperature environments. This is where heat-resistant tubing excels, crafted specifically to maintain structural integrity and performance when subjected to extreme heat. These tubes are typically made of materials such as silicone, fiberglass, PTFE (Polytetrafluoroethylene), and various metals, each tailored for specific applications and temperature thresholds.
Silicone tubing is highly revered for its flexibility and resistance to temperatures ranging from -100°F to 500°F. Its non-reactive nature also makes it an ideal choice for pharmaceutical and food-grade applications. Silicone tubing offers a balance of strength and pliability, which is why it’s often preferred in environments that demand durability without sacrificing flexibility.
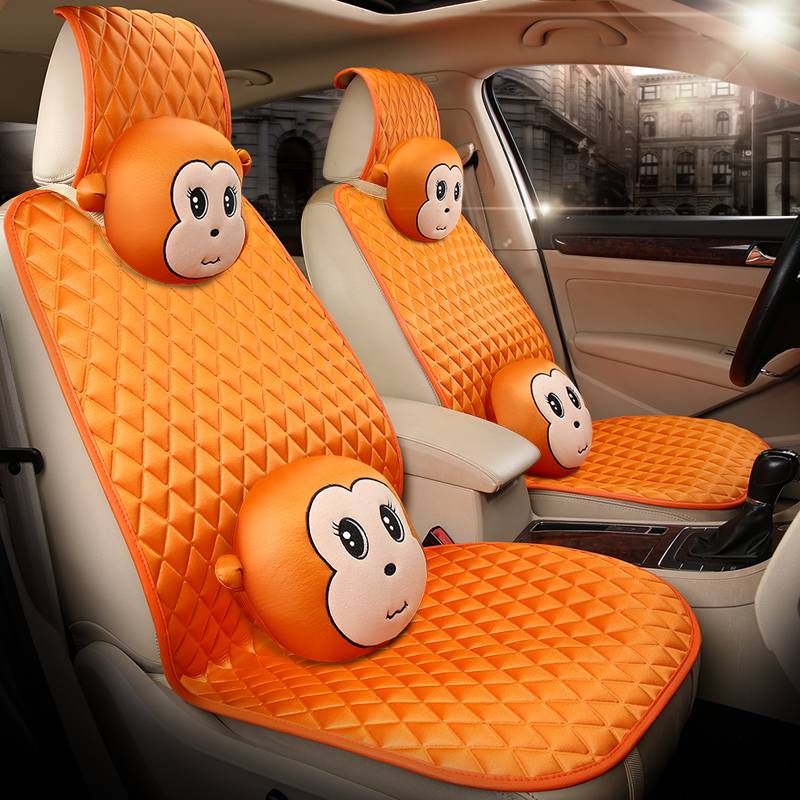
On the other hand, PTFE tubing is a marvel of chemical resistance and can withstand even more extreme temperatures, often up to 600°F. This type of tubing is crucial in applications involving corrosive substances. The non-stick nature of PTFE also adds a unique advantage, ensuring that residual materials do not adhere to the tubing walls, reducing maintenance and cleaning efforts.
Fiberglass tubing, impregnated with various resins, is another excellent option for heat resistance, often used in electrical insulation and found in transformers, motor gaskets, and other electrical components. This tubing can typically handle temperatures up to 1000°F, demonstrating incredible resistance without sacrificing structural integrity or electrical insulation properties.
The development and integration of heat-resistant tubes in industrial settings are not merely a matter of selecting the right material but also understanding the precise requirements of the application. Factors such as thermal expansion, environmental conditions, mechanical stress, and chemical exposure all influence the decision-making process. This expertise, gained from hands-on experience, ensures that the correct tubing is selected for each unique scenario, maximizing efficiency and safety.
heat resistant tubing
In aerospace, for instance, the requirements for heat-resistant tubing can be stringent, given the rapid temperature changes and high-stress conditions experienced during flight. Tubing materials here must adhere to rigorous standards to ensure reliability, as any failure could be catastrophic. Advanced materials such as titanium and high-temperature composites are often employed in this sector, reflecting the intersection of cutting-edge technology and practical application.
The automotive industry similarly relies heavily on heat-resistant tubing, particularly in exhaust systems and under-hood applications where temperatures can peak dramatically. Ensuring that tubing can withstand both extreme conditions and constant vibration requires a specialized understanding of material science and engineering principles.
Trust in heat-resistant tubing is built over time, rooted in consistent performance and rigorous testing. Manufacturers often subject these materials to extensive quality control tests, simulating worst-case scenarios to evaluate the reliability of their products. This process not only establishes credibility but also fortifies the user’s trust, knowing that the tubing has been thoroughly vetted for their specific application.
Authoritativeness in the realm of heat-resistant tubing also stems from compliance with international standards. Adhering to guidelines such as ISO and ASTM certifications underscores a commitment to quality and safety, essential for applications where human safety and significant investments are at stake.
For those looking to implement heat-resistant tubing in their operations, consulting with an expert vendor or supplier is advisable. These professionals can provide tailored insights and recommendations based on specific needs, ensuring that each component of the system works harmoniously under extreme conditions.
In conclusion, heat-resistant tubing is an indispensable element across various industries, integral to maintaining safety and efficiency in high-temperature environments. With the right expertise, these tubes offer reliable solutions, underscoring the importance of informed decision-making and adherence to industry standards. By leveraging these insights, businesses can optimize their operations, safeguarding both personnel and equipment against the challenges posed by extreme heat.