High pressure rubber hoses are essential components in various industries, ranging from construction and agriculture to automotive and manufacturing. Their primary function is to transport fluids and gases under high pressure conditions, making them crucial for operational efficiency and safety. In this article, we delve into the nuanced expertise required to select, maintain, and utilize these hoses effectively, leveraging industry experience and authoritative knowledge to ensure trustworthiness and reliability.

Understanding the Industry Standards
When it comes to high pressure rubber hoses, expertise in industry standards is paramount. Hoses must comply with rigorous safety and quality guidelines set forth by organizations such as the International Organization for Standardization (ISO) and the American Society for Testing and Materials (ASTM).
This adherence ensures they can handle specified pressure levels without failure. Manufacturers must provide documentation of compliance, including burst pressure ratings, temperature range, and compatibility with different chemicals and fluids.
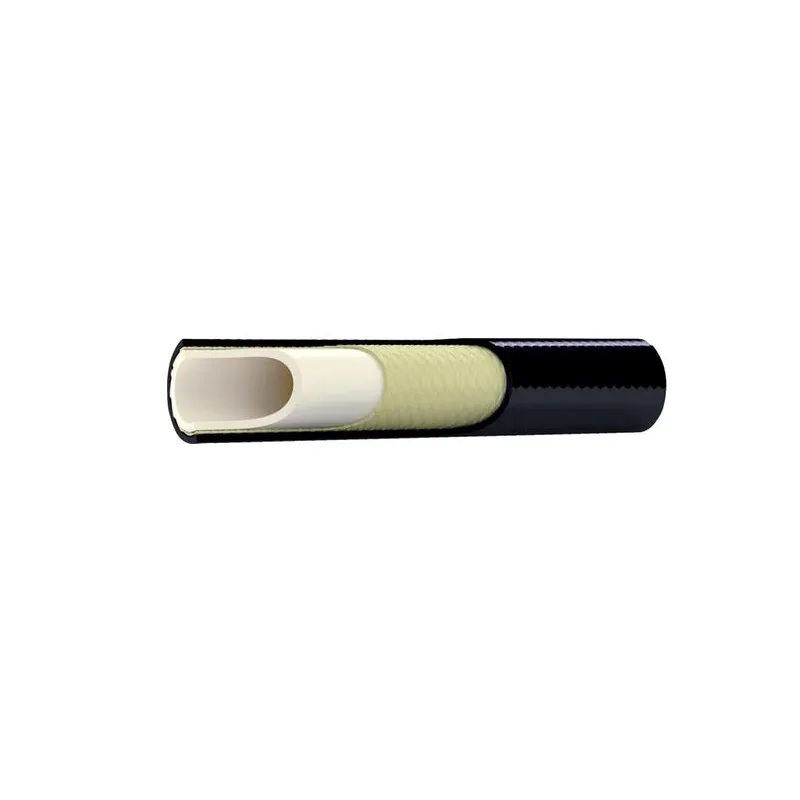
Material Science and Engineering
The expertise in material science is crucial when considering high pressure rubber hoses. These hoses are typically constructed from synthetic rubbers such as neoprene, EPDM, or nitrile, each offering unique properties. For instance, neoprene is resistant to chemicals and temperature variations, making it suitable for industrial applications, while EPDM is ideal for outdoor use due to its excellent weathering properties. Selecting the appropriate material is vital for ensuring durability, flexibility, and resistance to environmental factors.
Advanced Manufacturing Techniques
Technological advancements in manufacturing have enabled the production of high-quality rubber hoses that withstand intense pressure. Techniques such as extrusion and vulcanization are pivotal in enhancing the structural integrity of hoses. Manufacturers employ state-of-the-art equipment to ensure uniform thickness and strength across the hose, minimizing the risk of weak spots that could lead to leaks or bursts. Regular testing and quality control measures are integral to maintaining standards.
Real-World Applications and Experience
high pressure rubber hose
The application of high pressure rubber hoses in real-world scenarios offers valuable insights into their performance and reliability. Industries such as mining and oil and gas rely heavily on these hoses for operations that involve the transfer of hydraulic fluids and other pressurized substances. Field experience has shown that regular maintenance and timely replacement of worn hoses are critical in preventing downtime and accidents. Industry veterans recommend keeping an inventory of spare parts and conducting routine inspections to identify potential issues before they escalate.
Authoritative Voices in the Field
Gaining insights from authoritative voices in the hose manufacturing sector is instrumental in making informed decisions. Experts often emphasize the importance of working with certified suppliers who offer after-sales support and technical assistance. Trusted manufacturers provide detailed user manuals and training on proper installation techniques, ensuring that end-users have a comprehensive understanding of how to handle the hoses safely and effectively.
Building Trust Through Transparency
Trustworthiness in high pressure rubber hose solutions comes from transparency and reliable customer service. Clear communication about product specifications, warranty terms, and delivery schedules fosters a sense of credibility and confidence among users. Responsive customer support teams that offer prompt solutions to queries further add to the reliability of the supplier, making them a preferred choice for businesses seeking dependable suppliers.
Future Trends and Innovations
The future of high pressure rubber hoses looks promising with ongoing innovations focused on enhancing sustainability and performance. Eco-friendly materials that reduce environmental impact are gaining traction, while smart hoses equipped with sensors to monitor pressure variations are emerging. These advancements promise to offer businesses smarter, safer, and more efficient solutions, aligning with global trends towards digitalization and sustainability.
In conclusion, high pressure rubber hoses are more than just accessories; they are vital components requiring careful consideration and expertise. By understanding industry standards, investing in quality materials and manufacturing processes, and leveraging real-world experience, businesses can enhance their operations while maintaining safety and efficiency. With a focus on trustworthiness and innovation, the future of high pressure rubber hoses is set to align with evolving industrial needs and technological advancements.