Navigating the complex world of industrial equipment requires expertise, especially when it comes to selecting the right power hose for your operations. Industrial power hoses are indispensable in a variety of settings, ranging from manufacturing plants to cleaning operations. Understanding the nuances of this vital tool can optimize efficiency and safety while minimizing downtime.
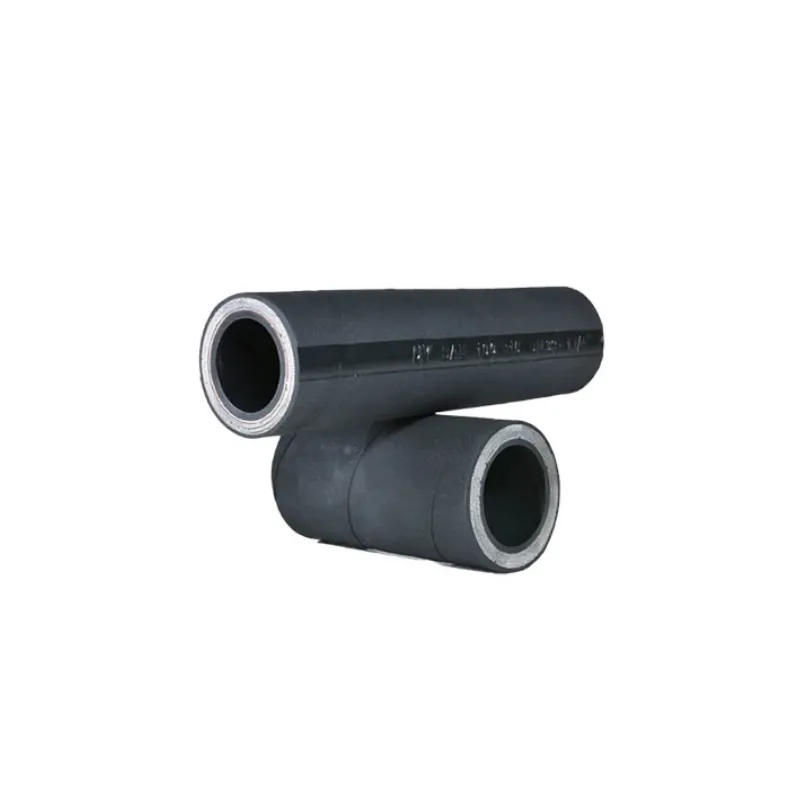
Industrial power hoses are engineered to withstand the rigorous demands of high-pressure applications. Their design often involves multiple layers of durable materials such as synthetic rubber, thermoplastics, and sometimes metallic reinforcement. These materials contribute to their resilience and durability under immense pressure, which is common in industrial settings.
When selecting an industrial power hose, flow rate and pressure rating demand careful consideration. Flow rate typically depends on the diameter of the hose, so choosing a hose with the appropriate size ensures optimal performance and energy efficiency. Pressure ratings, on the other hand, indicate the maximum pressure the hose can withstand. It's crucial to select a hose that matches or exceeds the required pressure load of your specific application to avoid failures or potential safety hazards.
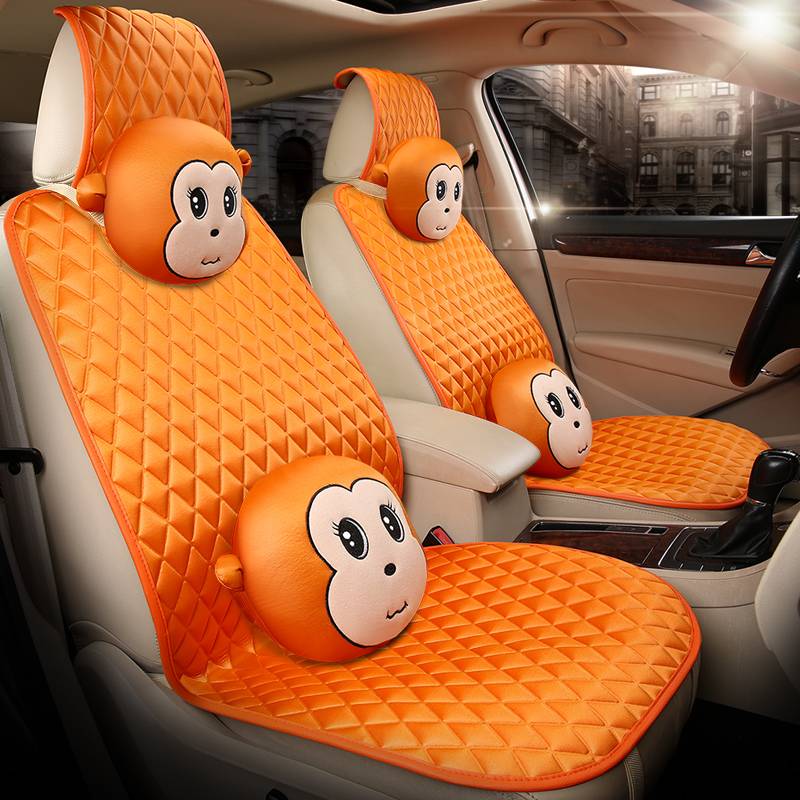
Another key factor in your selection process is the hose's resistance to the elements and chemicals. In industries where exposure to corrosive materials and extreme temperatures is inevitable, hoses made from advanced polymers or with special coatings offer superior longevity and reliability. Investing in hoses with strong abrasion resistance will significantly reduce the frequency of replacements, optimizing operational continuity and cost efficiency.
The importance of industry certifications should not be overlooked. It is imperative that power hoses meet standards such as ISO 18752 or SAE J517, which set benchmarks for safety and performance. Certification not only guarantees compliance with safety regulations but also assures users of the hose's reliability in compliance with industry standards.
industrial power hose
Effective maintenance is also critical to the longevity of industrial power hoses. Regular inspections for signs of wear, such as fraying, cracking, or bulging, can prevent catastrophic failures. Implementing a routine maintenance schedule with checks for proper fitting and connections can ensure safety and operational efficiency.
Selecting the appropriate coupling is equally essential for ensuring the full effectiveness of an industrial power hose. Incorrect or incompatible fittings can lead to leaks, energy loss, and potential system damage. Couplings must be matched in material and size to the hose and the equipment it attaches to, ensuring a secure, leak-free connection.
Expert users report that custom solutions can often provide significant advantages in specialized applications. Custom hoses tailored to specific industrial environments can incorporate unique material compositions or design adjustments to meet exact specifications, further enhancing effectiveness and lifespan.
The reputation of the manufacturer is a pivotal element to consider, as established manufacturers often have rigorous quality control measures and offer robust support and warranty options. Choosing a reputable brand can instill greater confidence in the product's reliability and performance.
To summarize, the decision-making process for selecting an industrial power hose should center around understanding the operational demands, the environment in which the hose will be used, and a rigorous assessment of product specifications and certifications. By leveraging industry expertise and focusing on these key factors, businesses can ensure they select the right industrial power hose, ultimately leading to enhanced productivity, safety, and business success.