Understanding the intricacies of pressure rubber hoses is crucial for anyone involved in industries such as automotive, construction, or engineering. Made from rubber, these hoses are specifically designed to handle high-pressure liquids and gases, making them indispensable in numerous settings.
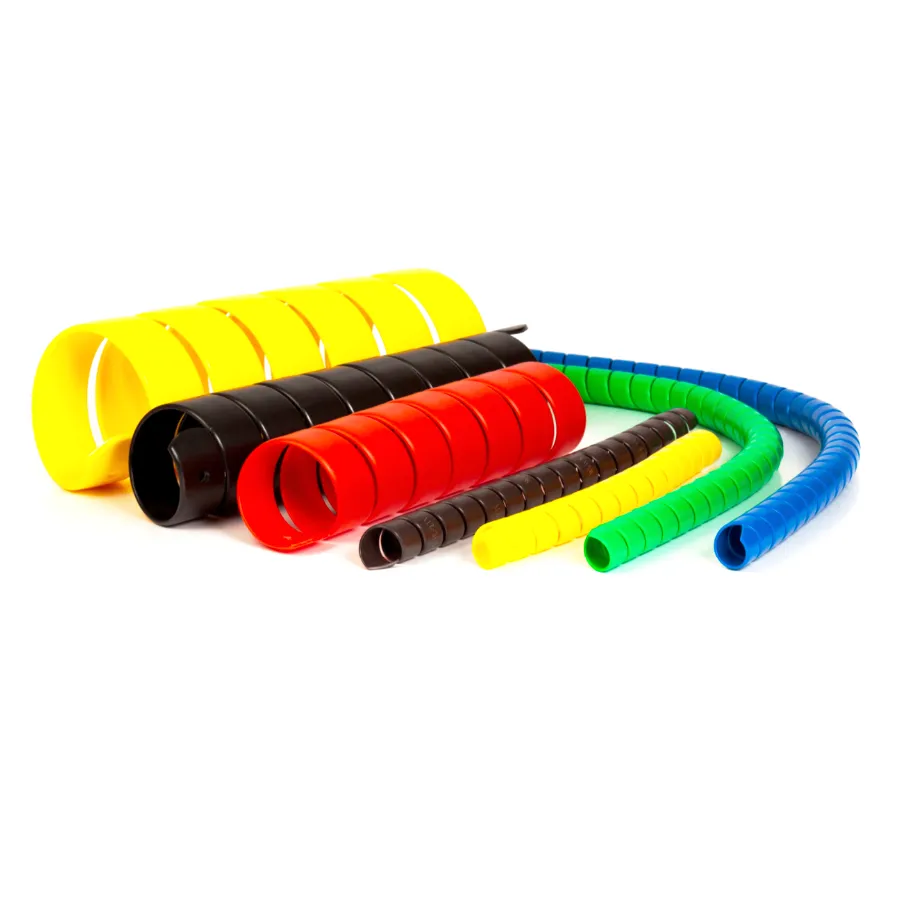
Pressure rubber hoses are celebrated for their flexibility, resilience, and ability to withstand extreme conditions. Unlike rigid pipes, they can be maneuvered easily into tight spaces, maintaining integrity and performance even in the harshest environments. The rubber composition is key, offering superb elasticity and durability, enabling the hoses to retain their shape and functionality over prolonged use.
From a professional standpoint, selecting the right pressure rubber hose can significantly impact operational efficiency and safety.
A common mistake is underestimating the pressure capacity of a hose. Each hose is rated for a specific pressure range; exceeding this can lead to devastating failures. It is essential to consult with hose manufacturers or industry experts to ascertain the maximum pressure tolerance suitable for your application.
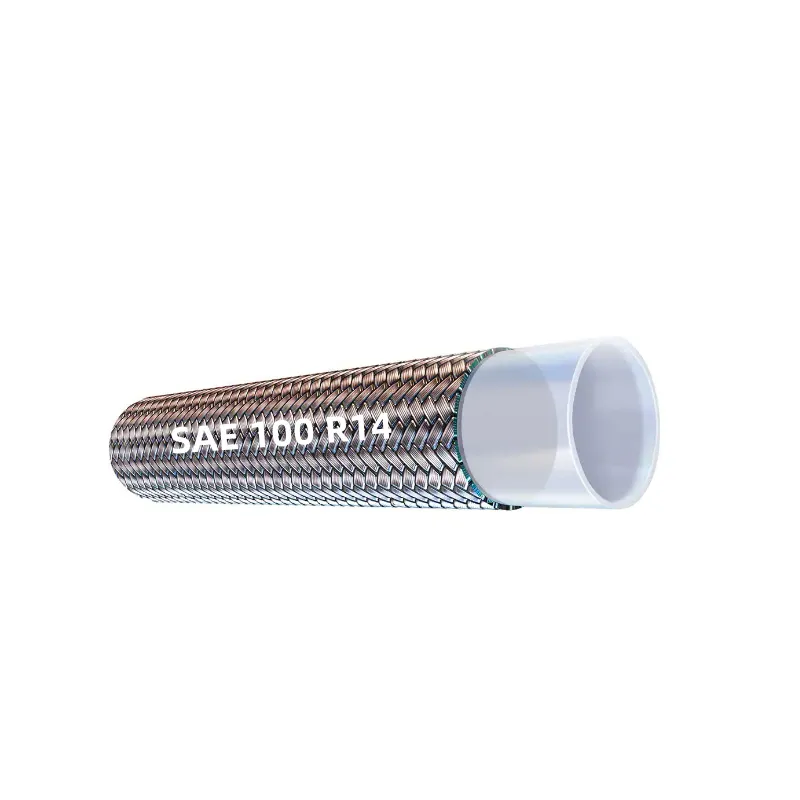
Furthermore, pressure rubber hoses are often fabricated with layers—commonly an inner tube, a reinforcement layer, and an outer cover. The inner tube must be compatible with the fluid or gas it will carry. For instance, oil-based substances require hoses with oil-resistant inner linings. Reinforcement layers add strength, typically using synthetic fibers or wires, contributing to the hose’s ability to endure high pressure without bursting. The outer cover protects against external damage from abrasion and environmental factors.
Proper maintenance and regular inspections are vital for ensuring the longevity and reliability of pressure rubber hoses. Industry guidelines recommend routine checks for wear and tear, cracks, or leaks. Immediate replacement is advised if any signs of degradation are found. This proactive approach not only ensures operational efficiency but also upholds crucial safety standards.
pressure rubber hose
Utilizing pressure rubber hoses effectively requires understanding their failure modes, such as fatigue and abrasion. Fatigue results from the continuous bending and flexing of the hose, where the reinforcement layer may weaken over time. Abrasion occurs when the hose is dragged across rough surfaces or exposed to sharp objects. Using protective sleeves or selecting hoses with abrasion-resistant covers can mitigate these risks.
The expertise in pressure rubber hoses also extends to understanding the specific needs of various industries. In automotive applications, for example, these hoses are integral in fuel supply systems, ensuring the safe transportation of gasoline under high pressure. In the construction industry, they’re employed in hydraulic systems, facilitating the operation of heavy machinery. Each use-case demands a thorough understanding of pressure dynamics and material compatibility.
As an authority on pressure rubber hoses, maintaining trust with stakeholders is paramount. Manufacturers must adhere to industry standards and rigorously test their products for quality assurance. Certifications from recognized entities serve as testament to a manufacturer’s commitment to quality and safety. End users should seek out these certified products to ensure they’re investing in reliable and trustworthy equipment.
In conclusion, possessing an in-depth knowledge of pressure rubber hoses can greatly affect both the operational effectiveness and safety of various sectors. It’s not just about choosing a hose—it’s about understanding its composition, capabilities, and the critical role it plays in your specific application. By doing so, industries can optimize their processes, enhance safety, and ensure long-term operational success.